Bauxite Residue Valorisation through Reductive Smelting: Coproduction of Pig Iron and Precursor for Inorganic Polymer Fire Resistant Building Materials ()

1. Introduction
The Bayer Process for the production of alumina from bauxite ore is characterized by low exergy efficiency and results in the production of significant amounts of dust-like, high alkalinity bauxite residues known as red mud. Currently red mud is produced almost at 1 to 1 mass ratio to metallurgical alumina and is disposed into sealed or unsealed artificial impoundments (landfills), leading to important environmental issues. Until the mid 1970s, marine discharge and landfilling were primarily used to dispose bauxite residue. So called dry stacking (even though residues are not entirely dry) and dry cake disposal have become the industry norm. Dry stacking involves thickening the bauxite residue to 48% - 55% solids, which subsequently is pumped through a sloped pipeline. Then, de-watering/air drying occurs before the next thin layer is released at the disposal area [1] . Bauxite residue emitted as a slurry-type paste of pH > 11, a high fine silt to clay size proportion, and a high sodium content. This leads to a preference for particle dispersion [2] , and as a result difficulties in handling and storing residue [3] [4] . Dry cake disposal involves thickening and pressure filtration, before using dump trucks to transfer residues to the storage area [1] . Pressure filtration not only results in a residue with lower water content, but also reduces losses of entrapped NaOH. This makes thickened/filtered residue more suitable for safer storage, transport and utilization in other industries (e.g. cement, iron). The current best practice in the industry is disposal in engineered bauxite residue disposal areas (BRDAs), using dry stacking and “mud farming” to aid dewatering for compaction/consolidation of residue at reduced alkalinity and leachate treatment [5] [6] [7] [8] . The proposed process utilizes an electric arc furnace (EAF) to achieve carbothermic reduction of the red mud waste without any pretreatment, producing pig iron and slag suitable for inorganic polymer-fire resistant building products.
2. Bauxite Residue Treatment
2.1. Current Management of Bauxite Residue in Greece
Mytilineos SA-Metallurgy Business Unit, Alumina and Aluminium plant (former Aluminium of Greece), is the only alumina refinery in Greece, processing each year about 1.8 Mt of bauxite ore (originating mainly from Greek bauxite mines), for the production of more than 800 kt of alumina and 750 ktons of BR. In 2006, the plant installed its first high-pressure filter press in Europe which produced a relatively dry BR. During the period 2006-2011 a total of 4 filter presses were installed and since 2012 all BR produced is filter-pressed and stored as a “dry” (moisture < 26%) by-product in an appropriate industrial landfill (Figure 1).
2.2. Pyrometallurgical Processing
The proposed bauxite residue treatment comprises four stages as shown schematically in Figure 2. The first stage is the residue drying stage, necessitated by the high remaining moisture content of residues (up 25% w/w), even when the best available upstream technology (filter press drying) is used for bauxite residue handling. This stage could occur in a double skin rotary kiln, using the heat content of the EAF hot off-gases or using waste heat from the alumina refinery itself (i.e. spent steam form the Bayer process). The second stage of the process focuses on EAF feed material preparation: dried bauxite residue, coke fines and appropriate fluxes are mixed in order to adjust the properties of the produced slag. This mixture is fed into the EAF, where raw materials undergo reductive smelting and are transformed into three distinct fluid phases: liquid slag, liquid pig iron and off-gases. The off-gases after heat exchange in the bauxite residue dryer are sent to a bag-house unit to remove dust particles prior to releasing them to the atmosphere. The dust collected is recycled in the feed material. The liquid pig iron and slag phases are separated by sequential pouring (or by continuous tapping) and the liquid slag is left to cool.
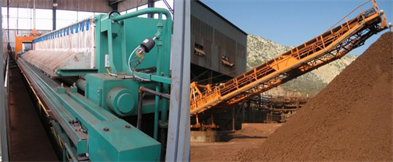
(a)
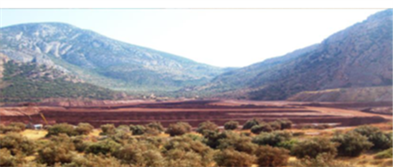
(b)
Figure 1. Filter press in operation and BR discharge (a); site of BR disposal in the plant (b).
![]()
Figure 2. The proposed production scheme.
Iron recovery from BR has been thoroughly investigated, and the developed technologies have been reviewed in several publications [9] [10] [11] [12] . The pyrometallurgical recovery of iron from the BR valorises approximately half of the Greek BR stream and at the same time alters the properties of the remaining material (slag) in such a way that it can be further processed, resulting in a zero solid/liquid waste process. Solid state reduction roasting [13] [14] [15] and reductive smelting [11] [16] are perhaps the most promising ones for producing either high-grade magnetite (Fe3O4) or metallic Fe. Through carbothermic reduction smelting using an electric arc furnace (EAF), the iron content of BR can be extracted as pig iron and sold as steel scrap substitute (price 300-EUR/t) to the secondary steel industry. BR trace elements like V, Cr, and Ni, which are of great value to the iron/steel industry, are collected in the produced melting iron phase. The EAF carbothermic smelting technology was developed in the EC-funded ENEXAL project [17] (Figure 3). The pig iron produced was suitable for the secondary steel industry as a 15 wt% scrap substitute in EAF processing. Larger BR pig iron utilization as scrap substitute would be disruptive to steel mill operations, as the minor elements of the BR pig iron (Cr, V, S, P, …) would produce steel outside of the required specifications for typical applications like steel rebars. However, given the size of the iron and steel market, the secondary steel industry could absorb all the BR pig iron even at low-scrap substitute rates. The overall exergy efficiency of the new bauxite exploitation schema increases from 3% in the conventional Bayer Process to 6 to 9% depending on the method used to produce the electricity needed to power the Electric Arc Furnace. Additionally, as the novel process enables the single step co-production of two highly valuable by-products (pig iron and pyrometallurgical slag), it has the potential to significantly increase the versatility and profit margin of the alumina producing industry.
![]()
Figure 3. ENEXAL flow sheet for 1 t of BR processing in dust treating EAF (batch processing trials, BR filter cake dried to below 2% in static bed dryer, dust collected in the bag filters has similar composition with the feed and can be recycled in the EAF.
As red mud is generally characterized by high iron content many attempts have been made to produce pig iron from red mud, but so far no economically viable solution has been found. The extremely fine particles of red mud require agglomeration prior to feeding in conventional reactors; their high alkaline nature is unsuitable for blast furnace reductive smelting and the low, when compared to iron ores, content in iron oxides makes the production of pig iron a cost ineffective process [18] .
The treatment has the capability of processing finely sized materials, notably below 1 mm in particle size (dust like), without any dusty material loss in the off-gas stream. As seen in Figure 4, the feeder can deliver the dusty raw materials directly into the “arc zones” of each of its three electrodes, where flash smelting takes place. This feeder is below the off-gas suction tube thereby preventing loss of material, and it feeds the reactor with small batches at appropriate time intervals in order to allow enough time for ventilation of the off-gases produced from the previous batch. The operation of the is controlled by a PLC control system, which, based on system-dependent programmable parameters predicted accurately by a proprietary thermodynamic model, can control impedance of the electric arc produced by the electrodes through the control of the positioning of the electrodes within the furnace influencing the energy input, the arc stability, the solid charge melting pattern and the electrode consumption. Therefore, this EAF technology is ideal for processing the dust-like red mud without any pretreatment or substantial energy losses, thus providing the proposed process with a significant industrial advantage.
Red mud chemical analysis used in the present work is given in Table 1.
Using carbon as a reducing agent, the red mud can undergo reductive smelting in the EAF producing pig iron and a slag. The pig iron produced in this way would amount to approximately 35% of the initial red mud charge, therefore pig iron production alone would not solve the industry’s waste disposal, as 65% of the red mud would still have to be disposed as EAF slag, while the expected turnover from selling such amounts of pig iron would not suffice to make for an economically viable process.
![]()
Figure 4. Schematic diagram and photograph of the innovative EAF melt reduction.
![]()
Table 1. Red mud used in the present work.
In order to design the process, the following operational parameters have to be established: melt temperature, required amount of coke and required amount of fluxes. As shown in the Ellingham diagram presented in Figure 5, the oxidation of carbon to CO(g) can reduce H2O, Fe2O3, Na2O, K2O at temperatures higher than 1000˚C, it can reduce SiO2 and TiO2 at temperatures higher than 1700˚C, MgO at temperatures higher than 1800˚C, while Al2O3 and CaO cannot be reduced at temperatures lower than 2000˚C. As the melting point of pure iron is 1537˚C the furnace operational temperature should be in the range of 1500˚C < T < 1700˚C in order to effectively reduce the iron in the red mud while avoiding silicon and titanium reductions. The furnace operational temperature for this study is therefore set at 1600˚C - 1700˚C and the reactions that are thermodynamically expected to take place and consume carbon are presented below:
(1)
(2)
(3)
(4)
The evolution of Na(g) and K(g) according to Equations (3) and (4) are highly unlikely as these oxides are in reality part of aluminosilicates complexes which are not as easily reduced. For instance, if sodium in red mud is found as nepheline (a logical assumption as nepheline is a part of cancrinite), then its reduction is thermodynamically unlikely.
(5)
Therefore, according to Equations (1) and (2) and the red mud chemical analysis given in Table 1 the amount of carbon required to reduce all iron and hydrogen content found in 1000 kg of red mud is 172.24 kg. To account for all possible side reactions an excess of 10% carbon will be used in the process (189.46 kg/1000kg red mud).
![]()
Figure 5. Ellingham diagram calculated from HSC Chemistry 6 software.
2.3. 1st Campaign
MYTILINEOS carried out the first bauxite residue smelting campaign in its pilot pyrometallurgical plant equipped with a 1 MVA electric arc furnace (EAF). The smelting tests utilized Bauxite Residue (BR), metallurgical coke and lime as raw materials, with the aim of producing cast iron and slag suitable for the creation of the “MudFire” construction materials. The recipe used adds relative to BR 30%wt and 18%wt Coke. At this loading, the C:Fe molar ratio is set at 2.2 (the stoichiometric demand is 1.5 for the reduction of Fe2O3 only, the excess being added to account for the other reduction taking place, including Na, Si, V, H2, Cr, Ni, etc.) and the molar ratio of CaO to Al2O3 is set to 3.4. In each test 300 kg of dry KB, 90 kg of CaO, 80 kg of starter slag (from previous test) and 54 kg of coke are melted at 1600˚C - 1700˚C and 90 kg of pig iron and 300 kg of slag are produced. Five tests were performed during this first campaign and the test results are detailed in the tables and graphs below. Average furnace energy consumption was 2233 kWh/t BR. A total of 487 kg of cast iron and 1259 kg of slag were produced. (Table 2 and Table 3)
3. Results
The pyrometallurgical slag produced was analysed to check the mineralogical phases produced so to proceed with the production of secondary building materials such as pavers and fire resistant boards using the novel inorganic polymer technology [19] [20] . In following graphs (Figures 6-11) XRD analysis from run#1 and #2 is presented.
The milled pyrometallurgical BR slag was treated further with geopolymer technology for the production of fire resistant building materials such as tiles, bricks and porous boards.
![]()
Figure 6. Mineralogical analysis of pyrometallurgical slag of test run #1.
![]()
Figure 7. Mineralogical analysis of pyrometallurgical slag of test run #2.
![]()
Figure 8. Elemental balance of raw materials used in test run #1.
![]()
Figure 9. Elemental balance of products produced from test run #1.
![]()
Table 2. Chemical analysis of pig iron and pyrometallurgical slag produced per run.
![]()
Table 3. Mineralogical phases of pyrometallurgical slag per test run.
![]()
(a) (b)
(c)
Figure 11. (a) crucibles and the slag, (b) slag after first crushing and (c) milled pyrometallurgical BR slag (d90 < 500 μm).
4. Light Weight Inorganic Polymers with Thermally Treated BR
The thermally treated bauxite residue is a good candidate to produce inorganic polymer building materials. The most common type of such secondary building materials are pavement blocks and fire resistant panels for the protection of the concrete and the building envelope [21] [22] .
In our study we produce light weight porous materials from thermal treated bauxite residue using 1 wt% fine aluminium powder (Alfa Aesar, 325 mesh, 99.5%) as chemical foaming agent [23] [24] . Thermally treated bauxite residue was milled to d90 80 μm before mixed with the liquid phase to a 2.9 solid to liquid ratio. The 2.9 solid to liquid ratio gave the best workable paste with enough water for the foaming agent to react and the lowest amount of water so to avoid cracking and bending during curing. As alkaline activator we use sodium hydroxide (Merck 99.5% purity, flakes) at [6M] giving the best mechanical properties (other molarities checked were 4.5, 5.5, 6.0, 6.5, 7.0 and 7.5 M [25] .
After 48 h curing in 60˚C the specimens were demoulded, tested for water stability, compressive and flexural strength at 7, 14 and 28 days. Finally, specimen was tested for its fire resistance according to ISO 834 fire curve in a small scale test (40 × 40 × 4 cm specimen fixed on 20 cm thick concrete slab with anchor fix. [26] [27] [28] (Figure 12).
![]()
Figure 12. ISO 834 fire test results of inorganic porous polymer.
The 28 days compressive strength and flexural strength was 4.3 MPa and 0.9 MPa respectively, density 1.135 Kg/m3 and specimen succeeded all fire test criteria (max interface temperature 159˚C, lower than 180˚C fail temperature), no concrete spalling, specimen retained integrity and no creeping or deformation was observed.
5. Conclusions
This manuscript mainly investigated thermal treatment of bauxite residue to produce two economic viable products: pig iron and inorganic polymer building material with fire resistant properties. After performing the investigation, the corresponding results can be obtained.
The bauxite residue smelting pilot plant successfully produced pig iron as well as pyrometallurgical slag rich in aluminum, silicon and calcium oxides. Although the unit is still in the pilot phase, the initial tests are considered successful and promising for further investigation and development. The chemical and mineralogical analysis of the resulting slag show an enrichment of the slag in aluminum and silicon, making it even more attractive for its use in the production of structural geopolymers.
Although the energy consumption for the co-production of pig iron and pyrometallurgical slag initially shows an increase in the environmental footprint, the final benefit from the reduction/reuse of bauxite residue as well as the possible profit from the production of commercial products leads to a neutral result. Also, the fututr use of renewable energy sources to generate electricity for the operation of the electric arc furnace will further reduce CO2 emissions, always in combination with the process optimization effort.
Acknowledgements
This research has received funding from the Operational Program “Competitiveness, Entrepreneurship & Innovation” (EPAnEK) and the Regional Operational Program of the Partnership and Cooperation Agreement (NSRF) for the period 2014-2020.