Development of Kaolin and Glass Fiber Reinforced Composites for Thermal Insulating Panels ()
1. Introduction
The utilization of kaolin, a naturally occurring clay mineral, in various industrial applications has been driven by its abundant presence in nature and unique properties. Over time, kaolin has found its way into thermal insulation materials, contributing to advancements in energy efficiency and sustainable construction practices. This research project focuses on exploring the potential of kaolin and glass fiber reinforced composites as a solution for thermally insulating panels. By combining the advantageous characteristics of kaolin and glass fibers, the objective is to enhance thermal insulation performance and offer a cost-effective alternative to conventional materials [1] . The origin of kaolin can be traced back to the gradual weathering of aluminum silicate minerals, such as feldspar and mica, spanning millions of years. This natural process leads to the formation of kaolin deposits commonly found in sedimentary rocks and soils. It is a conventional raw material for ceramics, porcelain, paper, coatings, rubber, plastics, fire-proof materials, chemicals, pesticides, medicines, textiles, petroleum, and building materials [2] . Due to its distinct crystal structure and particle morphology, kaolin exhibits excellent thermal insulation properties, characterized by low thermal conductivity, high specific heat capacity, and a low thermal expansion coefficient. These qualities make it an ideal candidate for various thermal insulation applications. Utilizing kaolin in thermal insulation materials has several advantages. Firstly, kaolin is a naturally occurring mineral, making it widely available and abundant in many regions. This availability helps reduce the environmental impact associated with extracting and producing alternative materials. Additionally, kaolin-based composites are relatively cost-effective compared to traditional insulating materials, making them economically viable for diverse applications [3] .
Composite materials synergistically combine the properties of two or more materials, surpassing what individual fibers or matrices can achieve alone. Fiber-reinforced composites have been successfully employed across various engineering applications for decades. Glass fiber-reinforced composites have been widely utilized in composite material manufacturing. The mechanical behavior of a fiber-reinforced composite relies on factors such as fiber strength and modulus, chemical stability, matrix strength, and the interface bonding that facilitates stress transfer between the fiber and matrix. By selecting suitable fiber compositions and orientations, the desired properties can be achieved. Glass fiber reinforced composites exhibit functional characteristics comparable to steel, with higher stiffness than aluminum, and a specific gravity one-quarter that of steel. Glass fibers are used to enhance the mechanical and tribological properties of composites. However, the high cost of polymers has been a limitation of their commercial applications. To address this, fillers have been employed to improve composite properties and reduce preparation and production costs [4] [5] .
Plant-based bio composites, particularly those reinforced with natural fibers, offer benefits such as low density, cost-effectiveness, low energy consumption, and the ability to neutralize CO2 emissions. One such natural fiber reinforcement is bamboo, which possesses characteristics such as affordability, high tensile strength, low density, and biodegradability. Bamboo exhibits a threefold increase in CO2 absorption and O2 production compared to other plants. In the pursuit of tough, semiductile, and high-strength composites, researchers have extensively explored natural fibers [6] [7] [8] . As a result, the adoption of natural fiber composites has been accelerated due to the demand for green technology and renewable composites. More attention is now being given to natural fiber composites as synthetic materials transition to more eco-friendly alternatives. It is imperative that further research be conducted in this field, as natural fibers are derived from renewable plant resources and are easily biodegradable [9] . Reinforcements can vary from high-cost, high-strength metal oxide or silicon carbide fibers to low-cost, abundant, and renewable natural fibers.
In this study, low-cost and readily available corn husk fibers were chosen as the reinforcement. The use of these agricultural byproducts as potential reinforcements for composite materials holds great promise, especially in developing countries where expensive and rare materials are not feasible or cost prohibitive. Natural cellulosic fibers have traditionally been used in papermaking but have more recently found integration into various composite forms, including polymer matrix composites [10] .
Alkaline solutions find wide-ranging industrial applications as binders, emulsifying agents, deflocculants. These solutions, based on potassium, possess complex structures comprising diverse monomeric and polymeric species. Alkali activated products were synthesized by activating kaolin clay with potassium silicate and hydroxide solutions combined with distilled water. These samples underwent long-term durability tests under different environmental and chemical conditions [10] [11] .
This research project aims to develop and characterize composites reinforced with kaolin and glass fibers for use in thermally insulating panels. By incorporating glass fibers, which offer high strength and stiffness, into the kaolin matrix, the intention is to enhance the mechanical integrity of the composites while preserving their excellent thermal insulation properties. The composition and manufacturing process will be optimized to achieve the desired balance between thermal performance and mechanical strength.
2. Experimental
2.1. Materials
2.1.1. Kaolin
Kaolin, a naturally occurring clay mineral, is primarily composed of aluminum silicate with the chemical formula Al2O2∙2SiO2∙2H2O. Its unique properties make it suitable for various industrial applications, including thermal insulation materials. The key among its advantages is its low thermal conductivity, which makes it an efficient insulator that reduces heat transfer and enhances energy efficiency in diverse applications. Additionally, kaolin’s high specific heat capacity enables it to effectively absorb and retain heat, further contributing to its thermal insulation capabilities [2] [12] . Kaolin, with its unique properties, availability, cost-effectiveness, and environmentally sustainable nature, serves as the binding matrix for reinforcing fibers like glass, corn husk, and bamboo, crucial for achieving the desired mechanical and thermal properties in composite materials. With a density of 2.52 g/cm3 and a diameter of 0.4 - 0.5 µm, kaolin boasts advantageous properties for thermal insulation applications. Kaolin was purchased from Thiele Kaolin Company for this project [13] .
2.1.2. Glass Fiber
Glass fibers are silica-based, lightweight, and high-strength fibers extensively used as reinforcement materials in composite applications due to their outstanding mechanical properties. The low density of glass fibers ensures that composites remain light, making them ideal for applications where weight reduction is vital [4] [14] . Among the various types of glass fibers available, the E-Glass Fiber was used in preparing the composite, featuring a density of 2.58 g/cm3, a length of 0.2 mm, and a diameter ranging from 9 to 14 µm. For this project, Glass fiber was purchased from the website “Faserverbundwerkstoffe Composite Technology” [15] .
2.1.3. Bamboo
Bamboo fibers exhibit high tensile strength, contributing to the structural integrity and load-bearing capacity of the composites. With a density of 0.72 g/cm3 and a diameter of 1 µm, bamboo fibers offer the advantage of keeping the composites lightweight, making them perfect for weight reduction in various applications. Furthermore, the biodegradability of bamboo fibers ensures that composites incorporating this material have a reduced environmental impact at the end of their life cycle [6] [7] [8] [9] . For this project, bamboo fiber was purchased from Amazon [16] .
2.1.4. Corn Husk
Corn husk fiber is a natural and renewable resource with significant potential in composite materials. As an environmentally friendly option, it naturally decomposes, thereby reducing the ecological impact of composite materials at the end of their life cycle. The accessibility of corn husk fiber as an agricultural byproduct makes it both cost-effective and sustainable as a reinforcement choice [17] [18] . By incorporating corn husk fibers, composites can experience improved mechanical properties. Corn husk fiber has a density of 1.49 g/cm3, a length ranging from 0.1 to 2 mm, and a diameter of 1 µm. Natural corn husks, readily available in the market, were used for this project.
2.2. Solutions
2.2.1. Potassium Silicate (K2SiO3)
Potassium silicate acts as a binder, potassium silicate effectively promotes strong adhesion between the kaolin matrix and reinforcing fibers in the composite material. Its alkaline nature aids in activating kaolin particles, leading to improved dispersion and homogeneity within the composite. Furthermore, potassium silicate enhances the chemical stability of the composite, providing resistance to moisture and chemical exposure. With its high refractive index, potassium silicate contributes to the optical properties of the composites, proving advantageous in certain applications [6] [11] [19] . The density of potassium silicate stands at 1.25 g/cm3. Potassium silicate was purchased from the Carl Roth Company for this project [20] .
2.2.2. Potassium Hydroxide (KOH)
Potassium hydroxide activates the kaolin particles by creating an alkaline environment and promoting their interaction with the reinforcing materials. By enhancing the chemical reactivity of the solutions, potassium hydroxide facilitates the curing process, ultimately contributing to the strength of the final composite [6] [11] [19] . With a density of 2.04 g/cm3, potassium hydroxide solutions are commercially available in various concentrations. For this project, 15% of the purest potassium hydroxide (KOH) was purchased from Subolab GmbH Feinund Industriechemie and utilized [21] .
2.2.3. Distilled Water
Distilled water removes impurities and minerals, resulting in a high-purity water source. The purity of distilled water ensures the integrity of the composite material, as it is free from impurities and contaminants. With a density of 1.00 g/cm3, distilled water is commercially available as a pure and standardized water source. Its specifications guarantee the absence of impurities or additives that could potentially impact the composite preparation process [11] [19] . Distilled water was sourced from the university lab at the Hochschule Kaiserslautern, Pirmasens Campus.
3. Hand-Lay-Up Process
The hand lay-up technique is a versatile, cost-effective, and widely used method for manufacturing composite materials. Unlike other manufacturing methods, hand lay-up does not necessitate specialized machinery, making it accessible for both small-scale and large-scale production of composite components and facilitates easy repairs and modifications. Another key benefit of the hand lay-up technique is its flexibility in fiber orientation [22] .
However, it’s important to note that the hand lay-up technique does require skilled labor for effective execution. While it offers significant advantages in terms of cost and adaptability, it can be time-consuming compared to automated or advanced manufacturing methods. Despite this, the technique remains popular and widely employed in various industries due to its ability to produce high-quality composite parts efficiently.
Below provided flow chart illustrates the outlined sequential steps that are systematically undertaken within the hand lay-up process to prepare the product.
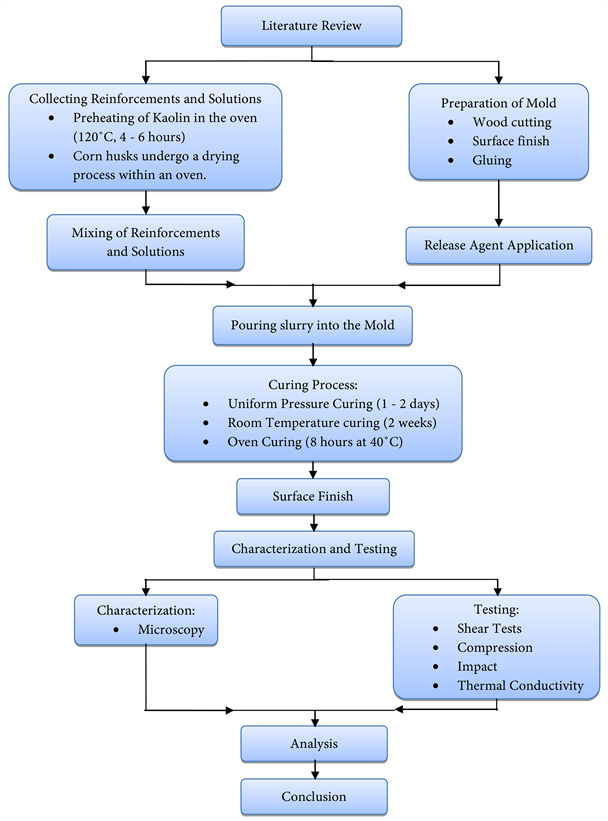
The combination of kaolin, glass fiber, corn husk fiber, and bamboo fiber in the composites creates a collaborative effect, enhancing thermal insulation performance while offering a lightweight, cost-effective, and environmentally sustainable solution for a wide range of applications. The hand-lay-up technique facilitates the preparation of these composites, allowing precise control over fiber orientation and matrix distribution and ensuring optimal performance in thermal insulation panels. Through the utilization of these specialized solutions during the composite preparation process, the project aims to achieve optimal bonding among the components. This will lead to composites with improved mechanical properties and exceptional thermal insulation performance.
In summary, the composite specimens were prepared using a comprehensive methodology. It involved preheating the kaolin, thorough mixing of reinforcements and solutions, controlled mold filling, precise curing processes, and the application of surface finish. This methodology ensured the creation of compact and homogeneous composite specimens ready for mechanical and thermal testing. Additionally, Table 1 provides the compositions of different specimens.
4. Mold Design
I skillfully crafted all three components from wood material obtained at the Hornbach retail company. To achieve the exact dimensions, I utilized a wood-cutting machine, and for the cylindrical shape, I employed a drill bit. These tools ensured precision and uniformity in the final products. The machines were conveniently accessible at the Hochschule Kaiserslautern, Pirmasens campus. For assembly, I used wood glue, which was also procured from the Hornbach retail company.

Figure A Figure B Figure C
![]()
Table 1. Compositions for different specimens.
In this project, different geometries of molds are used to fabricate specimens. Figure A illustrates the dimensions of a rectangular bar of 80 × 24 × 24 mm. Figure B showcases a cube with dimensions of 40 × 40 × 40 mm. Figure C represents a cylinder with a height of 18 mm and a diameter of 50 mm. These different geometries allowed us to assess a range of properties and behaviors in our experiments.
5. Mechanical and Thermal Properties Measurement
5.1. Shear Tests
Transverse shear tests were carried out using a Zwick Universal testing machine. Each composition was subjected to the creation of five standard specimens, each with dimensions of 80 × 24 × 24 mm (Figure A). The tests were conducted on these specimens with the following parameters: 1 MPa preload, 1 mm/min flexure modulus, and 1 mm/min test speed. The setup was adapted for a shear test by adjusting the machine configuration. This adaptation allowed for the reconfiguration of the Zwick Universal testing machine for shear testing while maintaining consistency in the experimental setup. Using the Test Xpert II testing software, measurements of transverse shear strength, flexural modulus, and elongation at break were obtained. The outcome value was calculated by averaging the results of the five tests.
5.2. Compression Tests
Compressive testing aims to assess a material’s response when subjected to compression forces. This type of testing enables the identification of a material’s behavior and its limits concerning ductile and brittle fracture under crushing loads. Compression tests play a crucial role in evaluating the elastic and compressive fracture properties of materials with low ductility or brittleness. The compression tests were conducted on the Zwick Universal Testing Machine. Cubic specimens with dimensions of 40 × 40 × 40 mm (Figure B) were used for these tests. The compression tests were carried out with specific parameters: 1 N preload, 1 mm/min compression modulus, 1 mm/min test speed, and a maximum force of 10 kN. Utilizing the Test Xpert III testing software, measurements of compression strength, compression modulus, and yield point were recorded.
5.3. Charpy Impact Tests
A RayRan advanced universal pendulum was utilized to conduct the Charpy impact test. This test assesses a material’s resistance to impact from a pendulum hammer with specific parameters: a velocity of 2.9 m/s, a hammer weight of 0.9510 kg, and an impact energy of 4 joules. The toughness of the material is determined by measuring the force required to fracture it when struck by the swinging pendulum. The specimen was supported horizontally and unclamped at both ends. The impact strength in kJ/m2 was calculated. This test was carried out on unnotched samples measuring 80 × 24 × 24 mm (Figure A).
5.4. Thermal Conductivity Tests
The thermal conductivity tests were performed using a custom-built measuring cell at the Institute of Polymer Technology at the University of Applied Sciences, Kaiserslautern. This setup follows the ASTM E 1225-04 standard and can measure cylindrical samples with a 50 mm diameter, whose thicknesses can vary from 2 to 50 mm. To conduct the test, cylindrical specimens of 18 mm in thickness and 50 mm in diameter (Figure C) were used. Prior to using the machine, it is essential to preheat the thermal conductivity measuring device for 8 hours or, if possible, overnight. You can achieve this by placing a reference sample in the device and applying 1.5 grams of conductivity paste on both the front and back sides. Once the preheating process is complete, the actual samples to be measured are tested using the machine.
5.5. Microscopic Analysis
Light microscopy, using an OLYMPUS BX40 device, was employed to investigate bonding characteristics in composite materials. Samples were placed on the stage and configured for magnified microstructure views. This allowed us to examine how the materials were spread out, how well they bonded together, and how uniform the microstructure was. This analysis provided valuable insights into the quality and integrity of composite materials.
6. Results and Discussions
6.1. Shear Tests
According to the data presented in Figure 1, Figure 2 and Table 2, there is an interesting relationship between the weight percentage of glass fiber and composite properties. As the weight percentage of glass fiber decreased, the flexural modulus increased, suggesting that the materials became stiffer. However, on the contrary, the transverse shear strength decreased when the glass fiber content was reduced. Figure 1 visually highlights this trend by demonstrating that composites with 15% glass fiber content exhibited the highest transverse shear strength, surpassing the values of composites with only 5% glass fiber composition.
![]()
Figure 1. Results obtained from the measurements of transverse shear strength.
![]()
Figure 2. Results obtained from the measurements of flexural modulus.
![]()
Table 2. Results of flexural modulus and transverse shear strength measurements.
6.2. Compression Tests
As per the information depicted in Figure 3, Figure 4 and Table 3, a clear trend emerges regarding the compression strength and compression modulus in relation to the weight percentage of glass fiber.
Notably, the compression modulus displayed an increase with a decrease in glass fiber content, indicating that composites with lower glass fiber percentages demonstrated higher resistance to deformation under compression. Conversely, the compression strength decreased as the glass fiber content was reduced, suggesting that composites with higher glass fiber percentages exhibited a better ability to withstand compression forces. Figure 3 provides a visual representation of the compression strength values, highlighting that composite containing 15% glass fiber content exhibited the highest strength values when compared to those composed of only 5% glass fiber.
6.3. Charpy Impact Tests
In Figure 5, the impact strength of the composites is shown, as the fiber content increased, the energy absorption rate also increased. This means that composites with higher glass fiber content demonstrated a greater ability to absorb energy upon impact, resulting in enhanced toughness. Figure 5 displays the impact strength values, indicating that composites containing 15% glass fiber content exhibited the highest impact strength values compared to those with only 5% glass fiber composition.
6.4. Thermal Conductivity Tests
Figure 6 presents the thermal conductivity of the composites. With an increase
![]()
Figure 3. Results obtained from the measurements of compression strength.
![]()
Figure 4. Results obtained from the measurements of compression modulus.
![]()
Figure 5. Results obtained from the measurements of impact strength.
![]()
Table 3. Results of compression modulus and strength measurements.
![]()
Figure 6. Results obtained from the measurements of thermal conductivity.
in the kaolin content, the thermal resistivity of the composites also increased. Composites with 30% kaolin content showed lower thermal conductivity than those with 40% kaolin content. This means that 30% kaolin content in the composites allows for better thermal conductivity.
6.5. Microscopy Tests
Upon microscopic examination, the microscopic analysis of sample 01 (Figure 7) showcased a superior microstructure characterized by well-dispersed reinforcing materials uniformly distributed within the polymer matrix. These images highlighted robust bonding interactions between the fillers and the matrix, contributing to enhanced mechanical properties and overall performance. These observations underscore the pivotal role of good dispersion and bonding in achieving desirable composite properties. In contrast, the images of sample 02 (Figure 8) revealed suboptimal dispersion of reinforcing elements within the polymer matrix. Poor distribution and clustering of filler particles were apparent, resulting in weak bonding between the matrix and fillers. Therefore, sample 02 exhibited reduced mechanical strength and performance compared to sample 01.
These findings emphasize the importance of precise material processing and optimizing composite fabrication to achieve a homogeneous and well-bonded structure.
7. Discussions of Results
According to the results, significant patterns in the performance of composites with variable kaolin and glass fiber contents have been observed. Flexural strength decreased as the weight percentage of kaolin increased, resulting in an increase in flexural modulus. Specifically, Kaolin 40% exhibited approximately 8.8% lower flexural strength but had an impressive 51.4% higher flexural modulus compared to Kaolin 30%. In the compression test, it has been found that as the glass fiber content decreased, the compression modulus increased, indicating higher resistance to deformation under compression. Kaolin 40% showed a
![]()
Figure 7. Optical microscopy test image of sample 01 at a 500 µm scale.
![]()
Figure 8. Optical microscopy test image of sample 02 at a 500 µm scale.
422% higher compression modulus, but a 49% lower compression strength compared to Kaolin 30%. Kaolin 30% has a higher compression strength, indicating its superior ability to withstand compressive forces. Kaolin 40% showed a lower impact resistance, only achieving 47.5% of the impact resistance observed in Kaolin 30%. Kaolin 30% outperformed Kaolin 40% in terms of impact resistance, being able to withstand a higher force before breaking or fracturing. In this research, it has been found out that composites with higher kaolin content exhibited lower thermal conductivity, that means improved thermal insulation properties. Specifically, 40% kaolin had a thermal conductivity approximately 66.67% lower than that of 30% kaolin. Glass fiber 15% displayed a superior microstructure with well-dispersed reinforcing materials and strong bonding characteristics. In contrast, Glass fiber 5% exhibited poor distribution and clustering of fillers, resulting in weaker mechanical properties.
In summary, Kaolin 30% is strong in compression strength, flexural strength, and impact resistance and has better bonding between the reinforcements, making it ideal for load-bearing applications and environments with potential impacts. Conversely, Kaolin 40% performs well in compression modulus and stiffness, making it suitable for scenarios demanding rigidity. Both compositions have excellent thermal insulation properties, with minor differences in thermal conductivity.
8. Conclusions
This research has unveiled valuable insights into the potential of kaolin and glass fiber-reinforced composites as thermal insulation materials, shedding light on their mechanical, thermal, and microstructural characteristics.
Glass fiber 15% has a superior microstructure with well-dispersed reinforcing materials and robust bonding characteristics. These observations highlight the importance of proper material processing and formulation optimization for achieving high-quality composites. The reason behind this is the balanced ratio of kaolin and glass fiber in the 2:1 formulation. This composition has a more uniform distribution of the reinforcing elements within the matrix, resulting in stronger interfacial bonding and enhanced mechanical properties. And the 8:1 ratio led to an excessive concentration of Kaolin, which caused clustering and improper dispersion of reinforcing materials, which in turn resulted in weaker bonding and inferior overall performance.
The adoption of natural and renewable reinforcements, such as corn husk and bamboo fibers, brings further significant environmental benefits for composite materials. This approach does not only reduce the reliance on synthetic materials but also contributes to more environmentally friendly and sustainable practices in composite manufacturing. The combination of potassium silicate and potassium hydroxide as binding agents has proven to be effective in activating kaolin and promoting adhesion among the constituent elements. These alkaline solutions exhibit impressive chemical stability, further bolstering the durability and cohesion of the composites.
9. Future Scope
Further research and experimentation could focus on optimizing the compositions to achieve a balance between mechanical strength, flexibility, impact resistance, and thermal conductivity. This could involve adjusting the proportions of kaolin, glass fiber, and other reinforcing materials to achieve the desired performance characteristics. Conducting finite element analysis and structural simulations can provide valuable insights into the behavior of the thermal insulation panels under various loading conditions. This can help to refine the design and composition choices for specific applications. Long-term durability testing, including exposure to various environmental conditions and ageing effects, will be essential to ensuring the reliability and performance of the thermal insulation panels over extended periods. Understanding their behavior in different real-world scenarios is crucial for practical applications. The hand lay-up technique used in this research is suitable for small-scale production. To make these composites viable for commercial applications, scaling up the manufacturing process using more automated methods should be explored. Moving towards real-world applications, additional testing, and certification according to industry standards will be necessary to validate the suitability and safety of the selected composition for thermal insulation panels. Consideration of the cost-effectiveness of each composition is vital for practical applications. A cost-benefit analysis should be conducted to determine which composition offers the best balance between performance and affordability.
Acknowledgements
The Institute for Plastics Technology West Palatinate (IKW) granted financial support for this paper, which the authors duly appreciate.