Regression Optimal Functional Control for a Kind of Unsymmetrical System ()
1. Introduction
As the most promising control theory, nonlinear system control theory has become the theme of modern control theory [1]. As a special kind of nonlinear system, the unsymmetrical system exists generally in modern industry, such as heating system, chemical system and mechanical system. The research on unsymmetrical system has attracted the attention of scholars since it was first proposed by Godfrey through steam experiment [2]. The characteristic of the unsymmetrical system is: the dynamic response of the system is completely different when the control input increases and decreases [3] [4] [5]. For the unsymmetrical system, if the controller is designed for a single linearized model of the whole system, the control effect is difficult to guarantee. At present, the study of unsymmetrical system has made some results. The modeling problem of unsymmetrical system is considered through an electronic nose system in [6]. Multiple identification methods and linearization methods have been proposed to approximate the unsymmetrical system in [7].
Most of the early research about unsymmetrical system focus on system linearization, but pay less attention to the design of control algorithms. With the advantages of multi-step prediction, rolling optimization and feedback correction, Regression Optimal Control (ROC) [8] [9] has made great contributions in dealing with problems of nonlinear constraints, system parameter uncertainty and actuator saturation [10] [11] [12] [13]. Based on the above studies, the regression optimal control algorithm is designed for the positive-negative model of the unsymmetrical system, and the control effect is obviously better than a single linearized model control of the whole system in [14] [15]. The regression optimal control remedies the error caused by the linearization process, but it is difficult to obtain the analytical solution of the controller.
As one of the classic ROC algorithms, Regression Optimal Functional Control (ROFC) has received wide attention. Different from other control algorithms, regression optimal functional control algorithm designs the controller as a linear combination of known basis functions, and the analytic solution of the controller can be obtained easily [16]. In [17], the regression optimal functional control based on multi-model switching is proposed, which greatly reduces the calculation and achieves good control effects. In [18], a Proportional Integral Derivative (PID) control algorithm based on regression optimal functional control idea is proposed, which not only contains the advantages of the regression optimal functional control algorithm, but also has the simple structure of the traditional PID controller. Considering that the calculation of ROFC is small and the analytical solution is easy to obtain, a regression optimal functional control algorithm for unsymmetrical system is proposed in this paper.
At the end of this section, the main contributions of this paper are summarized: (a) The regression optimal functional control algorithm is applied to unsymmetrical system. (b) The analytical solution of the controller is obtained by using the Minimum Principle.
2. Problem Statement and Preliminaries
Consider a class of unsymmetrical system:
(1)
where
is the system state,
is the control input,
is the system output. The control input
satisfies the following condition:
,
denotes the Euclidean norm. f and h are smooth functions with appropriate dimensions. And the determining function of the positive-negative model is given as follows:
(2)
This paper focuses on the control algorithm design for unsymmetrical system, so one of the linearization method in [15] is considered to obtain a linear representation of the unsymmetrical system. It is assumed that the origin is the equilibrium point of the system and that f and h are continuously differentiable at the origin. Expand the unsymmetrical system (1) at equilibrium point:
(3)
The above linearization method is considered to obtain a linear representation of the unsymmetrical system (1) in the positive and negative directions:
(4)
where
,
and
are constant parameter matrices with appropriate dimensions.
According to the recursive relationship, regression optimal model (4) can be written as:
(5)
(6)
where P is regression optimal step.
3. Main Results
3.1. Theory of Regression Optimal Functional Control
The design of the regression optimal functional control algorithm consists three steps as follows:
1) Multi-step prediction
Select appropriate regression optimal model for multi-step prediction:
(7)
2) Rolling optimization
Minimizing suitable performance indicator to calculate the control law:
(8)
By solving equation (8), we can get
. Only
is applied to the system.
3) Feedback correction
At the next time k + 1, according the error of the expected output and the systems output, the performance indicator J is reoptimized to calculate
.
3.2. Design of Regression Optimal Functional Controller
According to the idea of regression optimal functional control, we choose controller as:
(9)
where
is the weight coefficient of the linear combination of basis functions,
is a set of known basis functions, L is number of basis functions,
.
Let
,
,
.
Then,
can be expressed as:
(10)
Substituting Equation (10) into the regression optimal model (5) (6), and the regression optimal model can be written as:
(11)
with
and
3.3. Analysis of Performance Index
According to regression optimal model (11), the expected output is defined as:
, the optimization problem of performance index is proposed:
(12)
where
and
are the weight matrices of appropriate dimensions, and
,
.
Substituting Equation (10), (11) into Equation (12):
(13)
The necessary condition of minimum performance index is
, then:
(14)
(15)
Then, we select that
(16)
(17)
(18)
And the current moments control input can be expressed as:
(19)
3.4. Design of Switching Law
Define the increment of the control input as:
(20)
The principle of the system selects controller is as follows
(1) If
,
, then
;
(2) If
,
, then
;
(3) If
,
or
,
, then the system selects the controller that makes the performance index small: if
, then
; if
, then
.
Theorem 1. Consider unsymmetrical system (1), which can be approximated by positive-negative model (4), regression optimal functional controller (19) and switching law can ensure the closed loop system is stable.
Proof: According to the regression optimal functional control algorithm, the analytical solution of the controller
is obtained by satisfying condition of
, which can ensure that the subsystems performance indicator
is minimized, respectively.
If
(or
), continue to calculate
according to the above algorithm.
(1) When
,
, then
;
(2) When
,
, then
;
(3) When
,
or
,
, the system selects the controller that makes the performance index smaller:
If
then
,
;
If
then
,
.
To sum up, when switching does not occur, the regression optimal controller can stabilize the system; when switching occurs, the switching law is designed according to the principle of positive and negative model matching. Under the constraint of switching law, the controller switches reasonably between positive controller and negative controller. Finally, the stability of the closed-loop system is guaranteed by feedback correction and rolling optimization.
The executive strategy of the regression optimal functional control algorithm in this paper is given as follows:
Step 1: When
, the analytical solution of
is obtained by satisfying condition of
.
Step 2:
is given, define
. According to the principle of selecting positive or negative controller,
or
.
Step 3: If
(or
), continue to calculate
according to the above algorithm. (1) When
,
, then
; (2) When
,
, then
; (3) When
,
or
,
, the system selects the controller that makes the performance index smaller: if
, then
; if
, then
.
Step 4: Let
, go to the Step 1.
4. Simulation Examples
Consider three examples to verify the effectiveness of the algorithm in this paper:
Example 4.1 Consider the pH control of acid-alkali neutralization with strong nonlinearity and strong unsymmetry. The neutral reaction of strong acid and alkali is conducted in the continuous stirring reactor. Assuming that the reaction level is stable, a mathematical model of the reaction process in CSTR is established:
(21)
where
is the flow rate of the alkaline solution,
is the flow rate of the acid solution, V is the volume of the reactor,
is the difference between [OH−] and [H+], a is the concentration of the acid solution and b is the concentration of the alkaline solution, the water balance constant
.
With the flow rate of the alkaline solution
as the control input and pH value
as the output variable, consider the system has only one equilibrium point, the sampling time
, establish the positive-negative model:
(22)
where
,
,
,
,
,
are the corresponding values of each variable in the equilibrium state.
,
,
,
,
,
,
,
are the correction factor of the positive-negative model,
,
,
,
.
Select the wavelet functions as the basis functions of the regression optimization functional controller:
. The output of the three basis functions is shown in Figure 1.
The weight coefficients of the performance index
and
, regression optimal step
. The simulation results are shown in Figure 2, Figure 3.
The solid lines and the dotted lines represent the system response trajectories under regression optimal functional control and regression optimal control, respectively. When the system adopts the regression optimal functional control method, the system switches at
. When the system adopts the regression optimal control method, the system switches at
. Simulation results indicate that the regression optimal functional control algorithm can ensure the nonlinear unsymmetrical system state is ultimately stable. And compared with regression optimal controller, the regression optimal functional controller can bring the system state to steady faster.
Example 4.2 Consider a numerical example:
(23)
where
![]()
Figure 3. The trajectories of control input.
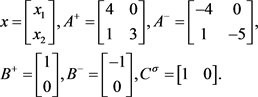
Next, the positive-negative model is discretized, and the sampling time is
. And the weight coefficient matrices of the performance indexs
and
, regression optimal step
. Choose wavelet functions as basis functions like Example 4.1. The simulation results are shown in Figures 4-6:
The solid lines and the dotted lines represent the system response trajectories under regression optimal functional control and regression optimal control, respectively. Both two control methods make the system switches at
. The simulation results show that the regression optimal functional control algorithm can ensure the system state is ultimately stable. And compared with regression optimal controller, the regression optimal functional controller has better control effect.
Example 4.3 (Tracking Problem) The system in Example 4.2 is considered, and the sampling time is
, regression optimal step
, the weight
coefficient matrices
and
. Choose wavelet functions as basis functions like Example 4.1. Let the expected output
, and the simulation results are shown in Figures 7-10:
In Figure 7, the solid line and the dotted line represent the system output and the expected output, respectively. The system switches at
,
and
. The simulation results show that the system under the regression
![]()
Figure 6. The trajectories of control input u.
optimal functional control can track the expected output in a short time.
5. Conclusion
In this paper, the regression optimal functional control algorithm for a class of unsymmetrical system is proposed. For the positive-negative model of unsymmetrical system, the regression optimal functional controller is designed. Based on the matching of the positive-negative model, the controller switches between positive controller and negative controller reasonably, which can make the system stable. The proposed algorithm has less computation and good control effect. Three simulation examples are used to verify the effectiveness of the proposed algorithm.
Date Availability
No data were used to support this study.
Acknowledgements
This research was supported by the Natural Science Foundation of China (Grant Nos. 61374004, 61773237, 61473170).