Analysis of Various Types Engineering Stripe Knit Fabrics of Bangladeshi Knit Industry ()
1. Introduction
Generally, the horizontal-coloured stripe designs are produced in course wise direction. According to the stripe design, there are two types of stripe fabrics:
A. Feeder stripe fabric: When maximum “2 - 3” colours are used to knit a stripe fabric where the stripe pattern length is lower than it is called feeder stripe (Figure 1). The feeder stripe designs are knitted on the general circular knitting machine. The main principle is to feed “2 - 3” colours on the feeders according to design and let the machine knit the required design. The knitting machine has a capacity for 108 cones of yarn. If you have inserted 8 black yarns to the feeder, with 100 cones of white yarn next. When knitting starts, you will see within the 2 inches repeat there is a black and white horizontal stripe. Feeder stripe designs can be made on Single jersey, Rib and Interlock machines.
![]()
Figure 1. Feeder stripe single jersey fabric.
B. Engineering stripe: When the size of the stripe repeat of the fabric is bigger than 2 inches which is beyond what the feeder stripe method can do, it is called engineering stripe. Engineering stripe designs are produced on a special type of circular knitting machine named auto stripe/engineering stripe machine. In the engineered stripe method, the machine is set to change threads at a certain time from a big repeat. This way the repeat can be of almost any size. However, the price of engineered stripe fabric is substantially higher.
It is produced in a special type of machine usually with four or six fingers arrangement called Auto Striper or Engineering Striper Machine. This type of machine was introduced to increase the scope of striping. The selection of each striping finger is affected by a programmable microcomputer in which the design information is fed. Solenoids above each striping finger are used to transmit striping instruction in accordance with the programme. It has an individual trapping and cutting of yarn at each finger.
The auto striper machine is equipped with a striper device called finger. The machine has usually 3, 4 or 6 fingers against each feeder. The fingers are centrally controlled either by a chain switch apparatus and rotating switch cams, or with the help of an electrical pre-selection and a mechanical rotary switch [1] [2].
For six colours engineering stripe, it’s very rare to find the same repeat length of various fabrics like single jersey, full feeder lycra single jersey, single lacoste fabrics. Our aim is to make sure that how those fabrics GSM, stitch length varies along with yarn count. That’s why we fixed how many courses would need for those respective fabrics to get the same numbers of repeat length.
In this experiment, we also investigated how stitch length, yarn count, yarn tension, machine rpm affects the fabric properties during production. Machine settings and proper maintenance before and after production is also a big factor during this experiment. Operation settings are also a big influential factor in this experiment.
In Bangladesh, most of the industries rarely practice these sorts of fabrics due to lack of orders. It is high time that we should enlist it priority to make acknowledgement of diversity into the fashion world through this kind of fabric.
2. Machine Specification
Engineering stripe single jersey knitting machine: This mentioned specified machine is used for the experiment.
Engineering stripe yarn path diagram: For the experiment, we need to concentrate into machine yarn path diagram of the followings:
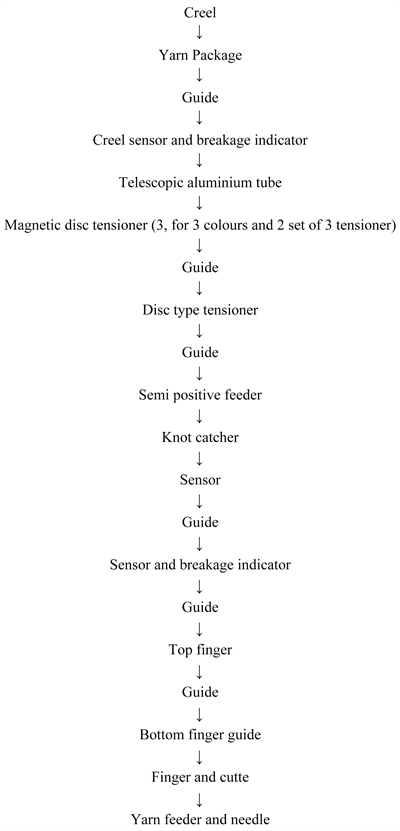
3. Additional Parts of Engineering Stripe Knitting Machine
•Creel stop motion • Semi-Positive feeder • Lycra yarn feeder • Additional tensioners • Finger • Finger box • Cutter • Actuator • Swing cam system.
Semi-positive feeder: Engineering Stripe machines have semi-positive yarn feeders (Figure 2). The thread path is given below [1] [2]:

Feeding principle: The striper feeder is based on the friction principle. The income yarn is guided through ceramic eyelets and a torsion rod and wound around the feed wheel for 1 - 2 circles. For 6 finger m/c, there are 2 feeding devices with 3 yarn wheels. These yarn feeders present torsion rod. By means of the friction between yarn and the wheel, the striper feeder provides a reliable yarn transport. Whenever a yarn is selected, it twists and moves away from wheel and thus gives sufficient tension for feeding. Other deselected rods remain close to wheel and where yarn tension is lower [3].
Finger: The yarn is fed with the help of finger motion. There are “4 - 6” fingers against each feeder. The finger works with the help of actuator. Selection of each finger is affected from control panel in which the design is fed. It has an individual clamping and cutting of yarn at each finger (Figure 3) [4] [5].
Finger box: All the fingers are attached in a box. For 4 fingers there are 4 metallic butts below of every finger box. The actuator selectors beat one of the fingers but to make it active (Figure 4).
Piezoelectric data actuator: An electronic actuator activates the powerful yet swift mechanical movement of finger in yarn change. The actuator has “4 - 6” selectors for four to six finger machines. The actuator is situated below the finger box and rotated with cylinder rpm. For 6 finger machine, 5 selectors will beat the 5 finger box butts. These 5 fingers will disable, only one finger will active. This one finger will take the selected thread. According to the program predetermined courses will be formed. Thus, another predetermined course will form (Figure 5).
4. Additional Features of Engineering Stripe Machine
Control panel for engineering stripe: Data acquisition system for machine control, recording and displaying the machine functions. Controller with 8 MB memory capacity and easy to select coloured yarn by means of the control panel, it is easy to change or select a coloured yarn, and modifies the stripe width. Error messages are shown on the display and can quickly be localized [1].
Design control system: The pattern data input through LCD touch panel. The computer program controls the changing for 4 or 6 colours striper fabric. With memory function, the computer control thread adjustment system can control many colour threads and can type:
1) Colour No.
2) Stripe No.
3) Course No. as you required [4] [5] [6].
Interchange ability: A quick-response actuator enables electronic selection at high speed. It can knit with various single knit structures such as Jersey, Pique, Lacoste, Terry as well as 1 × 1 Rib and 1 × 1 Interlock, etc [5] [7].
Durable and vertical mount fingers: The striper fingers are designed with independent yarn cutter with cancellation function. It is vertically mount for highest productivity, for easy maintenance. 4-colour and 6-colour stripers are built from similar platform and principles. They are used on both Single Jersey and Double Jersey machines [5] [8] [9].
Easy patterning software: It facilitates user in designing creative patterns. For greatest convenience of user, the patterns can be edited at the machine via the striper control panel [1] [10].
Engineering stripe machine set-up process [pailung]:
Step 1: Initially a new file is started, or previously available file is opened.
Step 2: Than a particular file no. is selected which is selected from an external device (pen drive) or an available file for editing. After touching ENT, it will skip to finger touch specification.
Step 3: Edited total numbers of courses and press ENT for the full pattern into the monitor.
Step 4: Edited total numbers of pattern and press ENT key.
Step 5: For 1st stripe of the pattern total no. of course is edited and press ENT.
Step 6: Now for every single stripe of the pattern the yarn colour is selected as A, B, C based on finger, edited, press ENT and later confirm the finger specification.
Step 7: Follow step-6 for the remaining stripes of the pattern.
Step 8: After entering the repeat, the folder has to be saved. Finally, the finger will work according to the program as provided into the monitor.
Knitting operation:
· The control panel sends control pulses to the actuator for the yarn insertion of selected yarn.
· There is a butt below every finger box.
· An actuator selector disconnects other butts and only one finger of finger box is selected.
· Actuator selects the finger according to the control panel command.
· There is a cutter with every finger box that cuts yarn after the completion of a course.
· The insertion process is implemented mechanically by means of cams.
· Optimally designed transmission ensures accurate insertion, clamping and cutting of the yarn, even at high machine working speeds [1] [11] [12].
Yarn changing process through finger:
Figuregives the aspect of a 4 fingers striper. We can see that the finger 1 is being selected and the finger 4 is being deselected. A cutting blade cuts the deselected yarn. Yarn change occurs in small zone (about 7 cm width) because in this zone 2 yarns work simultaneously during yarn change (Figure6) [1] [13] [14] [15].
5. Results & Discussion
Case study 1:
Fabric specification:
➢ Name: Engineering stripe normal single jersey;
➢ Order: Development sample;
➢ Finish día: Needle open;
➢ Finish gsm: 180;
➢ Stitch length: 2.95;
➢ Yarn count: 22 Ne.
Cam arrangement:
Here, Cam arrangement “K’’ indicates Knit Cam (for 1 & 2 butt needle).
From Table 1 found that, in six finger engineering stripe machines, in this development we initially installed the needle for engineering stripe single jersey fabric. As it used same amount length for each repeat which measured in centimetre (cm). In comparison with the other two developments, single jersey fabric consumed less revolution (Figure 7).
Case study 2:
Fabric specification:
➢ Name: Engineering stripe full feeder single jersey;
➢ Order: Development sample;
➢ Finish dia: Knife open;
➢ Finish gsm: 230;
➢ Stitch length: 3.30;
➢ Yarn count: 30 Ne;
➢ Lycra count: 40 denier;
➢ Lycra%: 8% (268 cm).
Cam Arrangement:
Here, Cam arrangement “K’’ indicates Knit Cam (for 1 & 2 butt needle).
![]()
Figure 7. Engineering stripe single jersey (6 Colours).
![]()
Table 1. Individual colour selection for engineering stripe single jersey fabric (6 Colours).
From Table 2 found that, in six finger engineering stripe machines, in this development we exchange installed needle for engineering stripe full feeder lycra single jersey fabric. In comparison with the other two developments, single jersey lycra fabric consumed much more revolution than other two fabric because of its lycra consumption. Before lycra adjustment, lycra instalment and lycra cm adjustment is also followed properly. Otherwise lycra drop, lycra cotton, lycra out problem could breakout simultaneously (Figure 8).
Case study 3:
Fabric specification:
➢ Name: Engineering stripe single lacoste;
➢ Order: Development sample
➢ Finish día: Knife open;
➢ Finish gsm: 160;
➢ Stitch length: 2.85;
➢ Yarn count: 22 Ne.
![]()
Table 2. Individual colour selection for engineering stripe full feeder lycra single jersey fabric (6 Colours).
![]()
Table 3. Individual colour selection for engineering stripe single lacoste fabric (6 Colours).
![]()
Figure 8. Engineering stripe full feeder lycra single jersey (6 Colours).
![]()
Figure 9. Engineering stripe single lacoste (6 Colours).
Cam arrangement:
Here, Cam arrangement “K’’ and “T” indicates Tuck and Knit Cam respectively (for 1 and 2 butt needle).
From Table 3 found that, in six finger engineering stripe machines, in this development we again installed the needle as like engineering stripe single jersey fabric. In comparison with other two developments, single jersey lacoste fabric consumed less revolution than lycra fabric and more than single jersey fabric. After needle installation cam arrangement need to be done (Figure 9).
6. Conclusion
In comparison, with other engineering stripe fabrics, 6 colours combo fabric is less produced in the knit industry of Bangladesh. In this experiment, we produced three different fabrics which have contained the same length of the repeat. But from fabric to fabric, the number of courses and gsm varies along with stitch length, yarn count, fabric dia, etc. Machine maintenance is also a big criterion during this experiment.
7. Future Scope
· Machine parameters should be investigated for more improvement;
· Software development for more added colours;
· To increase production efficiency.