1. Introduction
The Northern Ireland Water (NIW) potable water network delivers 585 million litres of drinking water each day through a system of reservoirs, water treatment works, pumping stations, and a network of water mains measuring 27,000 km longer than the entire Northern Ireland road network [1]. The pumps that convey water through parts of the overall network to homes and businesses are powered by electricity purchased on the commercial energy market and delivered via the national electricity grid. NIW is Northern Ireland’s largest single electricity user [2], and the energy required to pump water around the distribution network accounts for a significant amount NIW’s total energy use. The development of more efficient ways of delivery and maintaining water and wastewater assets has the potential to lead to significant financial savings for water utility providers. Pumping mains for water and wastewater are used where conveyance of the liquid by gravity is not an option due to the topography. This paper concentrates on pumped water mains referred to herein as pumped mains.
Aside from potential economic benefits, there are significant environmental benefits to be realised from a more energy efficient water distribution network. Addressing climate change is the defining issue of our time, and the water industry has a significant role to play in reducing carbon emissions at a local, national, and global level.
In financial year 2019/2020 NIW purchased just under 294 GWh of electricity at a cost of around £32 million, and over the same period NIW’s net operational carbon emissions amounted to 79,328 tCO2e [3]. NIW’s electricity consumption accounts for the vast majority of NIW’s carbon emissions [1], and water pumping accounts for 9% of NIW’s grid electricity consumption [4]. NIW’s stated goal is to become carbon neutral by 2050, and steps to achieve this goal include increasing electricity consumption from renewable sources to 100% by 2027 and planting 200,000 trees to improve carbon storage, with reducing consumption and improving energy efficiency key strategic themes [3].
The Republic of Ireland’s Department of the Environment, Climate and Communication’s Climate Action Plan [5] aims to halve national greenhouse gas emissions by 2030 and achieve net zero carbon emissions by 2050. Irish Water is the largest single electricity user in the public sector, consuming 1059.6 GWh in 2020 [6], and aims to achieve net zero carbon emissions by 2040 [7].
The water industry in the UK emits approximately 4 million tCO2 annually [8] and has a significant role to play in meeting national and international emissions reduction targets, and the development of more energy and carbon efficient pumped water main designs should form part of an industry wide effort to reduce CO2 emissions.
Recent research has examined the effect of water main diameter on chlorine decay [9], energy efficiency in large-scale distribution networks [10], the identification of inefficient assets within an existing network [11], and methods for quantifying carbon emissions associated with energy loss [12], but research on the long term financial and environmental impact of water main pipe diameter selection is lacking.
Value engineering as an approach is the analysis of systems with the aim of achieving essential functions at the lowest life cycle cost “consistent with required performance, reliability, quality, and safety” [13]. Research has highlighted how applying value engineering techniques applied thoroughly can lead to a large percentage reduction in overall project cost [14].
This paper summarises a research project on the effect of head loss on pumping cost and carbon emissions that examines how larger diameter pipes can result in long term financial and carbon emissions savings.
A series of sets of comparison design scenarios were set out allowing the head loss experienced by two pipe materials and three chosen diameters of water main pipe (150 mm, 250 mm, and 350 mm ductile iron; 125 mm, 225 mm, and 355 mm HPPE) to be demonstrated using the Colebrook White [15] and Darcy Weisbach [16] equations over a range of pipe lengths and elevation changes. For each comparison design scenario, the total required pumping power was determined, allowing a unit rate per kilowatt hour (p/kWh) for electricity to be used to determine the total cost of pumping over periods of 10, 20, and 30 years. The required pumping power for each design scenario was used to calculate total carbon emissions generated by pumping over 10, 20, and 30 year periods.
The comparison design scenarios were organised into 24 sets of three comparison designs. Each set of designs compares identical pipe materials, elevation changes, and pipe lengths, with only pipe diameter differing. Organising the comparison design scenarios in this way allows the head loss experienced by the three pipe diameters chosen to be compared across otherwise identical scenarios. A full list of comparison design scenarios is included in Appendix A.
A whole life costing analysis was carried out comparing the greater initial construction costs associated with constructing larger diameter water mains with potential pumping cost savings over the long term. This study has practical significance for pumping main design, there is clear demonstration that head loss is reduced through selecting larger pipe diameters. Even with the increased initial costs of using larger pipe diameters, in the long terms significant energy savings can be made, this reducing carbon footprints of the water industry. Value engineering solutions are required for pumping main design.
2. Method
The total head loss calculated for each comparison design scenario is summarised below, with the results organised into 24 sets of three design scenarios. For each set, the maximum flow rate for the smallest diameter pipe was established using the Colebrook White method. The velocity required to achieve this flow rate for the middle and larger diameter pipes was then calculated. The friction head and minor losses experienced by all pipe sizes when passing forward flow at the velocity required to achieve the maximum flow rate of the smaller diameter pipes was then determined. It was hypothesised that the middle and larger diameter pipes would be able to achieve the same flow rate as the smaller diameter pipe while experiencing less head loss, and therefore requiring less pumping power. Figure 1 below shows a graphical summary of all comparison design
![]()
Figure 1. Ductile iron—head loss (m) vs internal pipe diameter (mm).
scenarios featuring ductile iron pipes, showing internal pipe diameter plotted against head loss. Figure 2 below summarises all comparison design scenarios featuring HPPE pipes, again showing internal pipe diameter plotted against head loss.
Complete head loss calculation results are included in Appendix B. These results confirmed that for each comparison design scenario there is an inverse relationship between pipe diameter and total head loss, with increasing pipe diameter leading to decreasing total head loss. Head loss is the loss of pressure along a pipeline caused by the effect of a fluid’s viscosity along the internal pipe walls [17]. Larger diameter pipes have a larger cross sectional area, meaning less contact between the surface of water as it flows along a pipeline and the internal pipe walls. The results show that larger diameter water mains can deliver flow at the same rate as smaller diameter mains but at reduced velocity, and therefore less energy is needed to pump water at the required flow rate along larger diameter pipelines.
In the following section these results are interpreted to show how potential long term financial, energy, and carbon savings can be realised by selecting larger diameter water mains at design stage.
3. Analysis
The scenario testing results show that larger diameter pipes can be used to achieve the same flow rate as smaller diameter pipes while reducing the pumping power required.
The results show that the greater the static head (i.e. the greater the change in elevation over the length of a pipeline) and pipeline length, the more advantageous it is to use larger diameter pipes. The difference between the total head loss calculated for the smallest and largest diameter sets was found to increase as pipeline length and static head increased.
For Set 1, which featured a 500 m ductile iron pipe with a static head of 3 m, the head loss calculated for the largest diameter pipe was found to be 57.1% of that of smallest diameter pipe. By Set 23, which featured a 5000 m ductile iron pipe with a static head of 100 m, the head loss calculated for the largest diameter pipe was found to be 52.5% of that of the smallest diameter pipe.
![]()
Figure 2. HPPE—head loss (m) vs internal pipe diameter (mm).
For Set 2, which featured a 500 m HPPE pipe with a static head of 3 m, the head loss calculated for the largest diameter pipe was found to be 67.2% of that of smallest diameter pipe. By Set 24, which featured a 5000 m HPPE pipe with a static head of 100 m, the head loss calculated for the largest diameter pipe was found to be 62.5% of that of the smallest diameter pipe.
Using the Moody Diagram method carries a margin of error of approximately 4% [18], but a clear inverse relationship is established between pipe diameter and calculated total head loss.
3.1. Pumping Power Analysis
The energy required to overcome the total head loss determined for each comparison designed scenario was calculated as follows:
[19]
The results for ductile iron pipes are summarised in Figure 3 below, and the results for HPPE pipes are summarised in Figure 4 below.
Table 1 below shows the potential energy saving over 10, 20, and 30 year periods that could be realised by selecting the middle and largest sized diameter pipes for each set (250 mm and 350 mm for ductile iron, 225 mm and 355 mm nominal diameter for HPPE respectively) over the smallest diameter pipe (150 mm for ductile iron, 125 mm for HPPE).
These results show that there is a clear inverse relationship between pipe diameter and calculated water energy in kWh. The trend established by these results is that larger diameter pipes experience less total head loss than smaller diameter pipes when all other variables remain the same, meaning that less pumping power is required to overcome this head loss.
Table 1 below shows the potential long term energy savings that could be realised by selecting the middle diameter pipe in each set (highlighted in blue) and the largest diameter pipe in each set (highlighted in green) instead of the smallest diameter pipes tested. This demonstrates how an understanding of efficient design choices can lead to significant energy savings. This is most clearly illustrated in Set 23, which featured 5000 m ductile iron pipes with a static head of
![]()
Figure 3. Ductile iron—pumping power calculations summary.
![]()
Table 1. Potential energy savings summary.
![]()
Figure 4. HPPE—pumping power calculations summary.
100 m. Selecting a 250 mm diameter pipe instead of a 150 mm diameter pipe could lead to potential energy savings of over 9.24 GWh over a 30 year period. When a 350 mm diameter pipe is selected, potential energy savings over a 30 year period rise to 9.88 GWh.
3.2. Carbon Emissions Analysis
The results of the pumping power calculations for each comparison design scenario were used to calculate the total amount of CO2 emitted (in kg) by generating the electricity required to overcome the calculated total head loss as follows:
[20]
The results for ductile iron pipes are summarised in Figure 5 below, and the results for HPPE pipes are summarised in Figure 6 below.
Table 2 below shows the potential carbon emissions savings over 10, 20, and 30 year periods that could be realised by selecting the middle and largest sized diameter pipes for each set (250 mm and 350 mm for ductile iron, 225 mm and 355 mm nominal diameter for HPPE respectively) over the smallest diameter pipe (150 mm for ductile iron, 125 mm for HPPE).
The trend established in these results is that as less pumping power is required to overcome the total head loss encountered in larger diameter pipes, there is a significant reduction in the CO2 emitted through the process of generating the electricity required to pump water along larger diameter pipelines. It can therefore be concluded that for each set, the middle and largest diameter pipes created a smaller carbon footprint over the long term than the smallest diameter pipes. This is a result of less energy being required to overcome the total head loss experienced by larger diameter pipes compared to smaller diameter pipes.
Table 2 below summarises the extent to which CO2 emissions could be reduced by selecting the middle diameter pipe in each set (highlighted in blue) and the largest diameter pipe in each set (highlighted in green) over the smallest diameter pipes. Again these potential savings were most pronounced in Set 23, where selecting a 250 mm diameter pipe instead of a 150 mm diameter pipe could
![]()
Figure 5. Ductile iron—carbon emissions calculations summary.
![]()
Table 2. Potential carbon emissions savings summary.
![]()
Figure 6. HPPE—carbon emissions calculations summary.
lead to potential carbon emissions savings of over 2153 tonnes over a 30 year period, or over 2302 tonnes over the same period if a 350 mm diameter pipe is selected over a 150 mm diameter pipe.
3.3. Cost Saving Analysis
The results of the pumping power calculations for each comparison design scenario were then used to calculate the cost of purchasing the electricity required to power pumping equipment to overcome the total head loss by multiplying the unity rate of electricity paid by NIW in Q3 2021 (12.48 p/kWh inc. VAT) [21] by kWh usage, as follows:
The results for ductile iron pipes are summarised in Figure 7 below, and the results for HPPE pipes are summarised in Figure 8 below. Table 3 below shows the potential financial savings over 10, 20, and 30 year periods that could be realised by opting for the middle and largest sized diameter pipes for each set (250 mm and 350 mm for ductile iron, 225 mm and 355 mm nominal diameter for HPPE respectively) over the smallest diameter pipe (150 mm for ductile iron, 125 mm for HPPE).
These results show that significant financial savings can be made by selecting the larger diameter pipes over the smallest diameter pipe for each set of comparison design scenarios. Table 3 summarises the potential cost savings as a result of selecting the middle diameter pipe in each set (highlighted in blue) and the largest diameter pipe in each set (highlighted in green) over the smallest diameter pipes. In Set 23, selecting a 250 mm diameter pipe instead of a 150 mm diameter pipe could lead to potential savings of over £1.15 million over a 30 year period (over £38,000 a year), and over £1.23 million over 30 years (over £41,000 a year) if a 350 mm diameter pipe is selected rather than a 150 mm diameter pipe.
3.4. Construction Cost Analysis
The analysis so far has highlighted the financial and carbon emissions savings
![]()
Table 3. Potential financial savings summary.
![]()
Figure 7. Ductile iron—pumping cost calculations summary.
![]()
Figure 8. HPPE—pumping cost calculations summary.
that can be made by selecting large diameter water mains over smaller diameter ones. To determine whether this can result in long term financial savings it is necessary to consider whether the larger initial construction costs associated with laying larger diameter pipes can be offset by potential pumping cost savings.
The financial uplift associated with laying larger diameter pipes is a result of several factors, including the need to dig wider and deeper trenches during construction, resulting in a greater volume of trench bedding and backfill being required. The cost of pipes also increases as diameter increases, as more material is required for larger pipes.
Recently published industry data was used to indicatively assess, at a high level, whether the reduced cost of pumping larger diameter water mains could offset the larger initial capital outlay required over the long term.
This analysis can only be considered as a high level, indicative review. The average rate per meter, in GBP (£), for laying pipes of the materials and diameters tested as part of this research were taken from Spon’s Civil Engineering and Highway Price Book 2022 [22]. There are however many variables that can affect the construction costs of water main pipelines that will vary on a site specific basis, such as ground conditions, the presence of other services, design costs, and any land take that may be required, among other factors. These variables cannot be reflected accurately when using average rates collected on an industry-wide basis. In addition, the rates per metre selected (shown below) for 350 mm ductile iron, 125 mm HPPE, and 355 mm HPPE were not listed specifically, but were interpolated from rates given for other sizes.
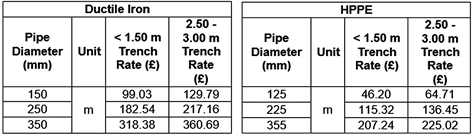
Two rates were selected for each pipe material and size – a rate for laying pipes in trenches less than 1.50 m in depth, and a rate for laying pipes in trenches between 2.50 and 3.0 m in depth. Of the range of trench depth rates available in the industry literature, these were selected as they represent reasonable “best case” and “worst case” scenarios. When there are no limiting factors to consider, it is desirable to lay water mains at depths of less than 1.50 m where possible to reduce costs. It is not however uncommon for water mains to be laid at depths of between 2.50 m and 3.0 m when necessary, but depths below this are usually avoided where at all possible due to greater costs and the risks associated with digging deeper trenches.
The construction cost uplift for laying the middle and largest diameter pipes when compared with the smallest diameter pipe for each set was then determined. This was then weighed against the potential calculated pumping cost savings over 10, 20, and 30 year periods.
Of the 24 sets of comparison design scenarios, eighteen were found to include an option (either the middle or largest diameter pipe, or both) which could result in pumping cost savings offsetting greater initial construction costs if selected in favour of the smallest diameter pipe, when laid at a depth of below 1.50 m and considered over a 20 year period. When considered over a 30 year period, 22 out of 24 sets were found to include a larger pipe option that could ultimately prove cheaper than selecting the smallest diameter pipe to meet a required flow rate.
When rates for laying pipes in trenches of 2.50 m to 3.0 m were assessed, eighteen out of 24 sets of comparison design scenarios were again found to include an option which could result in pumping cost savings offsetting greater initial construction costs over a 20 year period when a large diameter pipe is selected. Over a 30 year period, 22 out of 24 sets were again found to include a larger pipe option that could ultimately prove cheaper than selecting the smallest diameter pipe to meet a required flow rate.
The results show that there is a greater likelihood of pumping cost savings offsetting greater construction costs as pipe length and static head increase, and when potential savings are assessed over longer periods. The cost uplift of digging deeper trenches (2.50 - 3.0 m compared with depths above 1.50 m) did not reduce the number of sets found to include found to include a cheaper long term option than the smallest diameter pipe.
Based on the rates per metre selected for use in this analysis it can be concluded that selecting a larger diameter pipe will usually result in long term savings as a result of reduced pumping power requirement and therefore reduced pumping costs. It was found that more often than not, selecting the middle diameter pipe in each set was the most cost effective option. Even though the largest diameter pipes were found to require the least pumping power in each set of comparison designs, the greater construction costs associated with these could not usually be offset by the potential pumping power savings.
Even in sets which featured pipelines over lesser distances and elevation changes where it is found that selecting the smallest diameter pipe could be the financially cheapest option (Sets 1 & 2 over both trench depths), the cost of selecting either of the larger diameter pipes was found to be less than £90,000 over 30 years in each case. With this in mind, the value of potential carbon reductions should also be considered. Governments and water utility companies should consider whether it is worth meeting this larger cost to reduce carbon emission.
Recent research has confirmed that the occurrence of stagnation within a water distribution network is favourable for the multiplication of legionella [23]. Further research is needed to determine if the reduced flow rate experienced by larger diameter pipes can increase the likelihood of stagnant conditions occurring when compared with smaller diameter pipes, particularly during periods of low flow.
4. Conclusions
It is concluded that pumped mains of larger diameters can ultimately be more energy efficient and cost effective over the long term when selected in favour of smaller diameter pumped mains capable of delivering water at the same flow rate.
Scenario testing of 72 hypothetical water main designs has shown that there is a clear inverse relationship between total head loss and pipe diameter when all other variables remain the same. Larger diameter pipes can deliver water at the same rate as smaller diameter pipes but at much reduced velocities, leading to reduced total head loss. Analysis has shown that for ductile iron pipes the head loss experienced by the largest diameter pipeline of each set was on average 54.08% of that of the smallest diameter pipeline. For HPPE pipes, the largest diameter pipes experienced on average 63.98% of the total head loss of the smallest diameter pipes.
The pumping power required to overcome total head loss, in the form of water energy, was calculated using the scenario testing results for each hypothetical design which showed that the lower head loss experienced by the larger diameter pipes in each set resulted in a significantly reduced pumping power requirement. Sets featuring the greatest pipeline length and elevation change, or hydraulic gradient, showed the largest reduction in pumping power requirement as pipe diameter increased. Potential energy savings of up to 9.88 GWh over a 30 year period were found by selecting the largest diameter pipes over the smallest diameter pipes.
A method for calculating the carbon emitted through the process of generating the required pumping power for each comparison design scenario was applied to the water energy results. This has shown that the reduced pumping power requirement of larger diameter pipes led to a significant reduction in CO2 emissions, with potential carbon servings of over 2300 tCO2e over 30 years for the longest pipelines tested. Over time the carbon generated through electricity production will decline as the proportion of energy produced coming from renewable sources increases.
As required pumping power was found to decrease as diameter increased, potential long term cost savings were identified. The unit rate of electricity (p/kWh) paid by NIW was multiplied by the water energy required (kWh) for each design to get an hourly figure, which was then extrapolated over 10, 20, and 30 year periods. Potential savings of over £1.23 million over 30 years were identified if the largest diameter ductile iron pipe was selected over the smallest diameter pipe over the largest pipeline length tested.
For most of the hypothetical designs tested, it was found that the potential long term pumping cost savings that could be realised by using larger diameter water mains could offset the greater initial construction costs associated with larger diameter pipes. Hypothetical designs where this was not the case were over lesser distances and elevation changes, however the long term overall cost uplift associated with the larger diameters was found to be comparatively small – less than £90,000 over 30 years in each case.
As the largest single electricity user in Northern Ireland, NIW has pledged to achieve carbon neutrality by 2050 [3]. In financial year 2019/2020 NIW consumed approximately 294 GWh of grid electricity, a significant proportion of which was used to pump potable water around the public distribution network. To achieve publicly stated carbon emissions reduction targets, water utility providers must look at ways of further improving efficiency in all areas. This research shows the extent that considering the long term pumping requirements of different pipe sizes at design stage and selecting pipe size accordingly can contribute to the effort to reduce the carbon footprint of the water industry as a whole.
NIW spent approximately £32 million purchasing grid electricity in financial year 2019/2020 [3]. The economic constraints experienced by NIW as a result of chronic underfunding has a significant effect on funding available for key water and wastewater projects, effecting regional economic growth as a whole [24]. The financial savings that could be realised by designing water infrastructure to operate as efficiently as possible could free significant capital that could be invested in, for example, failing wastewater infrastructure and improving environmental protection.
Potential energy, carbon, and cost savings were calculated over 10, 20, and 30 year periods to highlight the potential long term savings that could be realised by selecting larger diameter pipes during the water main design process. These time frames were chosen as net zero emissions targets will be approaching over the next 20 - 30 years. NIW has committed to achieving carbon neutrality by 2050 [3], while Irish Water aims to achieve this by 2040 [7]. This research has shown how changes to design choices in the present day can help water companies to achieve these goals.
Value engineering has traditionally been viewed from a financial perspective, but the potential for carbon emissions reductions over the long term should also be considered as adding value. Governments and water utility companies should consider whether it is worth meeting this larger cost to reduce carbon emissions where pumping cost savings were not found to offset the greater construction cost associated with larger diameter pipes.
Appendix A. Comparison Design Scenarios
Appendix B. Head loss Calculations Summary