Leveraging Robust Artificial Intelligence for Mechatronic Product Development—A Literature Review ()
1. Introduction
Mechatronic product development is a multifaceted and intricate endeavor that encompasses a wide range of disciplines, including, among others, mechanical engineering, electrical engineering, control theory and software engineering. This holistic approach combines various fields to create innovative and sophisticated products that integrate mechanical components, electronic circuitry, intelligent control systems, and software algorithms [1] .
Traditionally, human experts have been at the forefront of mechatronic product development, providing their expertise and insights into decision-making processes and managing knowledge within their domain. Their extensive experience and intuition have been instrumental in tackling complex design challenges and optimizing the performance of mechatronic systems [2] .
For the sustainable operation of AI systems, a data-driven mindset must be anchored throughout the company.
Beate Hofer, CIO, Volkswagen AG.
However, the landscape of mechatronic product development is rapidly evolving, driven by the remarkable progress in AI technologies, like for example [3] and [4] show. The technology has emerged as a powerful development force capable of augmenting and supporting the entire lifecycle of mechatronic product development. With its ability to analyze vast amounts of data, recognize patterns, and learn from examples, AI holds immense potential to revolutionize the industry, as described in [5] .
To harness the AI potential in practical applications, various approaches have been undertaken to address specific identified aspects and their associated potentials. For instance, [6] conducted research into collaborative electro-mechanical actuator development for aircraft applications. This endeavor involved a complex, multi-physical system comprising diverse components such as DC motors, microcontroller units, gearboxes, and others. The development process inherently involves multiple domains, making it conducive to the utilization of AI to facilitate more effective knowledge exchange and interface architecture design.
Another critical aspect of mechatronic product development is the multi-criteria optimization of components. [7] undertook this challenge to explore the extent to which AI can enhance this process. Their investigation centered on the development of a 2 Degrees of Freedom robot as a case study. The outcome of their work resulted in the creation of an AI-based tool designed to aid in optimizing various design parameters and constraints, as well as assisting in the subsequent evaluation of these optimizations.
This paper therefore explores the existing literature for the key aspects regarding the use of context sensible and robust support through artificial intelligence in Mechatronic Product Development, such as including new possible domain linking, expert knowledge replacement and robust prediction quality.
Specifically, this raises the question: what extent is artificial intelligence already finding its way into the field of virtual product development, and what findings are there in this regard?
2. Process-Oriented Mechatronic Product Development with AI-Support
The V-Model is a software development and testing framework that underscores a systematic methodology for ensuring the quality and dependability of software systems. It is depicted in the shape of a “V” to visually represent the interrelation between diverse development and testing stages, where each stage has a corresponding testing phase on the opposing side of the V. In the sphere of mechatronic product development, the V-Model assumes significant relevance, as it facilitates the organized development and validation of all constituent components and their interconnections [8] .
2.1. The V-Cycle and Its Phases in Detail
Figure 1 presents the V-Model in its current version, following VDI 2206. However, it has been edited with regard to the potential use of artificial intelligence, introducing an additional green-colored strand that highlights the potential for each phase of development.
The cycle starts with an already established business model (Checkpoint 1). Subsequently, the phase begins with the goal of specification. This phase involves gathering and analyzing the requirements for the mechatronic system, which include mechanical, electronic, and software aspects. These requirements serve as the foundation for the entire development process. In this phase, AI can already provide support through automated requirement capture, Natural Language Processing, or early risk detection, among other means [9] [10] [11] [12] .
Upon completing this phase and reaching Checkpoint 2, the specification phase, the System Architecture phase begins. This phase considers the integration of mechanical, electronic, and software components. The V-Model helps ensure that the design aligns with the requirements and that all elements are compatible. It concludes with the established architecture (Checkpoint 3). Support from AI can manifest in design automation, appropriate simulation models, potential error detection, collaboration, and knowledge management, to name a few which can be found for example in [13] [14] [15] and [16] .
The visually lengthiest phase is the implementation of system elements. This section involves developing individual subsystems, such as the mechanical structure, electronic components, and software modules. Each of these subsystems
![]()
Figure 1. Process concept for the context-sensitive and robust use of AI in the V-model [8] related product development.
undergoes its own design, coding, and testing. Here, AI can assume important roles related to translation, interpretation, and prediction approaches. Successful completion culminates in Checkpoint 4, Implementation [17] [18] [19] .
The subsequent stage describes system integration and verification. This phase is crucial in mechatronics, where various components must work together seamlessly. The V-Model emphasizes the integration of mechanical, electronic, and software subsystems and verifies that they function as intended. Once integration is fulfilled, it concludes at Checkpoint 5. AI can offer vital support in interface automation and, if necessary, enable real-time monitoring. [20] [21] and [22] , among other sources, highlight these aspects.
The last phase encompasses validation and transition. This ensures that each component and subsystem meets its requirements and performs as expected. Additionally, it ensures that the integrated mechatronic system functions correctly. It ends with completion at Checkpoint 6. Important aspects here include intelligent test selection and associated test data management. AI, for instance, can select the most relevant test cases and assist in the creation and management of test data by generating synthetic data or anonymizing and masking real data [8] [23] [24] .
The following section provides a detailed overview of how artificial intelligence can support each of these phases in concrete terms.
2.2. Detailed Support Options through the AI Techniques
One significant application of AI in mechatronic product development is its role as a comprehensive database. By harnessing AI techniques, such as machine learning and knowledge representation, vast amounts of information can be efficiently stored, organized, and retrieved. This AI-powered database becomes a valuable resource, enabling engineers to access a wealth of knowledge, previous designs, simulations, test results, and best practices—available more quickly and understandably through the AI itself. This centralized knowledge repository not only accelerates the design process but also facilitates collaboration among interdisciplinary teams by providing a shared platform for information exchange [25] .
All phases of our innovation and development process are characterized by a high degree of interdisciplinarity.
Patricia Rennert, Head of Industry Solutions, Porsche Digital GmbH.
Moreover, AI can contribute to the decision-making process by offering intelligent recommendations and insights. By analyzing historical data, performance metrics, and design constraints, AI algorithms can suggest design improvements, optimize parameterization, and propose alternative solutions. This collaborative approach between AI and human experts enables a more efficient exploration of the design space and helps identify optimal solutions in a shorter timeframe. This is seen for example in [26] .
Furthermore, AI techniques can be utilized for modeling and simulation, allowing engineers to predict the behavior and performance of mechatronic systems under various operating conditions, as shown [27] . By simulating and iterating designs in a virtual environment, engineers can evaluate different design alternatives, identify potential issues, and refine the system before physical prototypes are built. This virtual prototyping reduces costs, shortens development cycles, and mitigates risks associated with physical prototyping.
Another area where AI can make a significant impact is in the field of intelligent control systems. Through advanced algorithms, AI can optimize control strategies, adapt to changing environments, and learn from system responses. By integrating AI-driven control algorithms, mechatronic systems can exhibit enhanced performance, fault tolerance, and adaptability, allowing them to operate efficiently in dynamic and uncertain conditions [28] .
However, it is important to note that while AI offers tremendous potential, human expertise and judgment remain invaluable in mechatronic product development. The collaboration between AI and human experts creates a symbiotic relationship, where AI complements human creativity, intuition, and domain knowledge. The human expert’s ability to contextualize information, interpret complex trade-offs, and consider ethical and societal implications ensures that AI-driven solutions align with the desired objectives and constraints. An overview can be found, for example, in [29] .
In conclusion, the integration of AI in mechatronic product development represents a significant leap forward in the field. By leveraging AI as a powerful database, decision support system, and modeling tool, engineers can tap into an unprecedented wealth of knowledge and accelerate the development of innovative mechatronic systems. The combined efforts of AI and human expertise hold the potential to drive remarkable advancements, unlocking new possibilities and transforming the way mechatronic products are conceived, designed, and deployed.
3. Key Aspects to Be Examined in the Literature
Below is a detailed list of the criteria that are of particular relevance in the presented methodology. These include both unavoidable aspects (robustness of predictions) as well as potentials that arise as a result, presenting new opportunities. It is possible that the respective literature to be presented may only cover a portion of these aspects, and there may also be various other effects that are not listed here.
3.1. Consideration of the Holistic Cycle
Mechatronic product development follows a holistic development cycle, encompassing various stages from concept ideation to prototyping, testing, and deployment. A standard procedure model for this is, for example, the V-model according to VDI 2206, to be seen in [8] and described in detail above.
AI databases can capture and store information from each stage of the development process, enabling a comprehensive knowledge repository. This facilitates knowledge sharing, reuse, and continuous improvement across different projects, ensuring that lessons learned and best practices are incorporated into future development cycles.
3.2. Domain Linking
AI-based databases can facilitate the integration and linking of various domains involved in mechatronic product development. By incorporating data from mechanics, electronics, controls, and software, AI systems can establish connections between these domains, providing a comprehensive view of the entire system. Further, you can also help to synchronize the processes and even translate different domain languages appropriately.
This integration enables synergistic decision-making, enhanced interoperability, and the identification of potential design conflicts or trade-offs that might otherwise go unnoticed, like for example described in [30] .
3.3. Replacement for Human Expert Knowledge
AI databases have the potential to replace or complement human expert knowledge in mechatronic product development. By training AI models on big data and domain-specific knowledge, these systems can learn from human experts and mimic their decision-making processes. This enables consistent and reliable recommendations and helps automate certain tasks, leading to higher efficiency and accelerated development cycles.
It should be emphasized that especially the interaction seems to be extremely valuable and as a consequence new potentials appear. “Machine learning (ML) models are increasingly being used in application domains that often involve working together with human experts. In this context, it can be advantageous to defer certain instances to a single human expert when they are difficult to predict for the ML model” [31] .
3.4. Differentiation from Non-Relevant Knowledge
Artificial intelligence databases enable the differentiation between relevant and non-relevant knowledge, a matter of paramount importance due to the prevailing knowledge explosion and the data deluge surrounding product development, both of which must be effectively managed. By employing advanced search algorithms, natural language processing, and semantic analysis, information-based databases can filter and prioritize relevant information from a vast reservoir of data, like for example seen in [32] .
As a result, this ensures that engineers and designers can access the most pertinent knowledge tailored to their needs, thereby reducing information overload and facilitating informed decision-making. Simultaneously, the successful disregard of irrelevant knowledge leads to shortened development cycles and inevitably enhances the quality of outcomes.
3.5. Consideration of Knowledge Gaps
One of the challenges in mechatronic product development is addressing knowledge gaps. AI databases can help identify and bridge these gaps by suggesting areas where further research, data collection, or experimentation is needed. By analyzing existing data and identifying patterns of missing or incomplete information, these databases can guide researchers and engineers in filling knowledge gaps, leading to a more comprehensive understanding of the system and improved decision-making [33] .
One possible approach is to use Knowledge Graphs. A knowledge graph is a network of interconnected nodes (entities) that represent concepts and relationships between them. Each node in the graph can have attributes (properties) that store specific information. In this way, it is possible to develop an ontology for the knowledge graph, i.e., a formal specification of the types of entities, relationships, and properties that can exist in it. This ontology will provide a common vocabulary and structure for the information in the graph, making it easier to understand and use.
After creating the knowledge graph, you can use machine learning algorithms and techniques to infer missing information and complete the graph. These algorithms can detect implicit relationships, predict new connections, and fill in gaps based on existing data.
Subsequently, it is still possible to validate the data integrated into the knowledge graph to ensure accuracy and reliability. Incorrect or outdated information can lead to faulty conclusions and decisions. Implement quality assurance processes to regularly review and update data [25] [34] [35] [36] .
On a technical level, this is achieved by data imputation methods. This is a technique used to fill in missing values in a data set. To fill knowledge gaps through data imputation, the missing values must be estimated based on existing data [37] .
There are a few steps to go through for this:
The starting point is to identify the variables with missing data in the data set. It is important to understand the magnitude and patterns of the missing data before proceeding to impute the data. Next, several techniques exist for imputing data, each with its strengths and limitations. The key here is to find appropriate imputation methods based on the nature of the missing data and the characteristics of the data set. Some common imputation methods include mean/median imputation, regression imputation, and k-nearest neighbor (k-NN) imputation [38] [39] .
Next, evaluate the accuracy and validity of the imputation method chosen. Techniques such as cross-validation are used for this purpose to assess how well the imputed values match the true, observed values. Finally, use the selected imputation method to fill in the missing values in the data set [40] .
3.6. Robustness of Prediction Quality
When utilizing ANNs for prediction purposes, it is essential to assess the reliability of the model’s predictions. “However, basic neural networks do not deliver certainty estimates or suffer from over or under confidence. Many researchers have been working on understanding and quantifying uncertainty in a neural network’s prediction. As a result, different types and sources of uncertainty have been identified and a variety of approaches to measure and quantify uncertainty in neural networks have been proposed” [41] .
In order to tackle this issue and mitigate undesired consequences associated with the reliability of artificial intelligence (AI), it is imperative to quantify and predict the uncertainties inherent in neural networks. The primary objective is to calculate an additional output value that reflects the network’s level of confidence in its predictions, with higher values indicating greater uncertainty. This, in turn, serves to inform users about potential deviations [41] [42] .
Before delving into the analysis of uncertainty within Artificial Neural Networks (ANNs), it is essential to gain a comprehensive understanding of the underlying sources of these uncertainties. Categorizing uncertainties based on their origins can significantly aid in this comprehension, specifically distinguishing between data uncertainty and model uncertainty. This differentiation allows us to gain valuable insights into the nature of uncertainties within the context of ANNs [43] .
3.7. Consideration of Optimization Proposals with AI
AI databases provide opportunities for optimization proposals in mechatronic product development. By analyzing vast amounts of data, these databases can identify areas for improvement, optimization, and performance enhancement. They can suggest design modifications, parameter adjustments, or even propose entirely new design alternatives based on historical data, simulations, and performance benchmarks. This streamlines the design process, enhances product quality, and accelerates time-to-market.
3.8. Application to One or More Proofs of Concept
If new concepts and methods arise within the source selection, it appears reasonable in all cases to validate them through one or more proofs of concept. The goal is to validate feasibility, verify methodology, provide experimental validation, evaluate performance, illustrate innovation, and promote reproducibility and transparency. It plays a crucial role in establishing the credibility and impact of the research findings within the scientific community. However, it should be emphasized that this may not be applicable in all cases. Therefore, this feature is expected to be present in some papers but not in all.
4. Consideration of the Theory Deficit
In this section, we will assess the compiled literature selection based on the categories introduced earlier. The evaluation will be conducted using a scheme that involves five levels of consideration. Each level is represented by a circle that is filled to a certain extent, indicating the degree of attention given to the specific characteristic. Here is a breakdown of the evaluation scheme:
1) No consideration of the characteristic (circle not filled)
At this level, the literature selection shows no attention or focus on the particular characteristic introduced earlier. The characteristic is not addressed or mentioned in any meaningful way in the literature.
2) Rudimentary consideration (circle filled to a quarter)
In this level of evaluation, the literature selection demonstrates only a basic acknowledgment of the characteristic. There might be minor references or brief discussions related to the category, but without substantial depth or analysis.
3) Balanced consideration (circle half filled)
At this stage, the literature selection exhibits a moderate and well-rounded consideration of the characteristic. The authors have given reasonable attention to the category, discussing various aspects and providing a relatively comprehensive analysis.
4) High focus on the category (circle filled to three quarters)
In this level of evaluation, the literature selection shows a substantial focus on the specific characteristic introduced earlier. The majority of the content is dedicated to exploring the category in depth, offering valuable insights and extensive discussions.
5) Holistic consideration of the category (circle completely filled)
At the highest level of evaluation, the literature selection exemplifies a comprehensive and all-encompassing consideration of the characteristic. The authors have thoroughly analyzed and extensively covered the category, leaving no major aspects untouched. The literature demonstrates a profound understanding and valuable contributions to the field regarding the specific characteristic.
After completing the evaluation using the above scheme, a summary of the findings will be presented in the subsequent step. This summary will highlight the distribution of literature across the different levels of consideration and provide an overall assessment of the literature selection’s coverage and depth concerning the introduced categories. The goal is to gain valuable insights into how well the literature addresses and contributes to the understanding of each characteristic and its relevance to the broader context of the study.
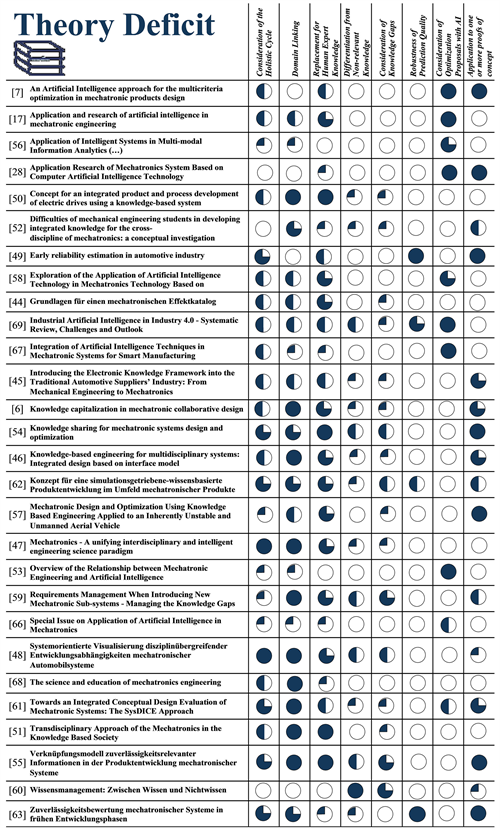
5. Evaluation and Conclusions
It can be observed that all the sources consulted extensively address the predetermined aspects considered in this study. However, it is noteworthy that none of the selected papers comprehensively cover all the categories, nor do they do so in proportionate measure.
The consideration of the holistic cycle is subject to substantial examination by a significant number of sources, such as [7] [44] [45] and [46] . However, it is worth noting that certain sources, such as [47] and [48] , delve deep into the intricate details, providing a comprehensive exploration of this particular feature. This extensive examination of the holistic cycle can be attributed, in part, to the pivotal role product development cycles play in mechatronic research.
[48] points out precisely this circumstance and emphasizes “Strategies of product development are therefore similar in the pursuit of goal-oriented courses of action, system-oriented thinking and the design of procedures and behaviors” [Strategien der Produktentwicklung gleichen sich daher in der Verfolgung zielorientierter Handlungsweisen, einem systemorientierten Denken sowie der Gestaltung von Vorgehens- und Verhaltensweisen].
[47] underlines the aspects again and shows that the statement also works in the other direction: “Finally, adopting and understanding the philosophy of mechatronics as a way of thinking […] would be great assets to be considered by other engineering and nonengineering disciplines, as it would empower them with strength and competence.” Thus, the mechatronic way of acting can also positively influence general product development.
Similar patterns emerge in the category of domain linking. While there are only a few sources where this aspect remains unexplored, as exemplified by [49] and [7] , it is crucial to recognize that these resources are inherently specialized and do not possess a fundamental focus. Conversely, there is a considerable body of literature, including [6] [50] and [51] , that extensively examines the domain linking concept.
In this regard, [51] provides a highly detailed description of the importance of mechatronics as a transdisciplinary field that incorporates diverse facets of knowledge and creativity, adjusting to the dynamic demands of a complex and swiftly changing world. To illustrate this, they present various key points, such as the Synergistic-Generative Transdisciplinary Model and the Transdisciplinary Knowledge Search Window.
[50] emphasizes that “A local optimum in one particular domain or even the whole product design does not necessarily represent the global optimum regarding all the participating domains and processes.” Further, the authors confirm that “Due to the interdisciplinary expertise needed for an integrated product and process development, it is necessary to manage the extensive domain knowledge by means of a sophisticated information system.”
The investigation pertaining to the replacement for human expert knowledge represents the final category that exhibits a substantial frequency of exploration. Certain sources provide a rudimentary analysis of this topic, such as [28] , [52] and [53] . Conversely, authors of publications such as [54] and [55] place significant emphasis on this aspect, meticulously examining its implications.
[54] describes parts of the problem as follows: “Systems Engineering Modeling makes clear improvement in the mechatronic process. However, a gap still exists between the descriptive models of SysML and expert models. Consequently, the information of a fine granular level, such as parameters and constraints, is generally not taken into account. In fact, they are encapsulated inside experts’ models and not shared. This knowledge is a key factor in achieving multidisciplinary collaboration.” The presented methodology to counteract this circumstance is the presented Knowledge Configuration Model, whose goal is “to extract critical data which is necessary for the collaboration (Grundstein (2000)). This data is then stored in the form of parameters and expert rules.”
The category of differentiation from non-relevant knowledge follows a distinct pattern. Numerous sources neglect to address this aspect, which may be attributable to either thematic irrelevance or no particular focus is placed on this type of observation. Instances of the former behavior can be observed in sources like [56] and [28] , while the latter is evident in sources such as [57] and [58] . However, a limited number of resources provide a more comprehensive exploration of this criterion, as exemplified by [59] and [48] . Nevertheless, a truly exhaustive examination is only accomplished by [60] .
The last source presupposes for this first of all an existential recognition of the not-knowing. Depending on the interpretation, it is possible that the non-knowledge is understood as irrational knowledge or even pure ignorance. However, this interpretation would not be conducive for the consideration within mechatronic product development, since here instead an ignorance competence is aimed at, i.e. the conscious handling of incomplete knowledge. The same is also emphasized by [60] the statement “completeness of knowledge is not attainable” [Vollständigkeit des Wissens ist nicht erreichbar]. Going further, the author speaks of a principled boundary between our knowledge in the present and the knowledge of the future world in the realm of procedural processes. “This boundary is the not-knowing, be it as not-yet-knowing, be it as principally not-knowing” [Diese Grenze ist das Nichtwissen, sei es als noch-nicht-Wissen, sei es als prinzipielle Nichtwissbares].
A similar trend can be observed in the consideration of knowledge gaps. A significant number of sources fail to address this criterion, as seen in examples like [49] and [53] . Some attention is devoted to this aspect in sources like [44] [50] and [61] . However, a comprehensive treatment of this topic according to the established criteria is absent. Only [55] [59] and [60] encompass the subject matter in a broader sense.
According to [59] , knowledge gaps occur at the interface between the Knowledge Value Stream (KVS) and the Product Value Stream (PVS). “The question that is posed is simply ‘what is known’ and ‘what is needed to be known in order to reduce the risks prior to initiating the PVS for a certain product’ […] The closing of the knowledge gap is characterized by analytical activities to see in which intervals of requirements different principal solutions work and by doing so see which are viable for the current projects requirements.” As a solution, a collection of recommendations for action emerges, which contains corresponding suggestions for the respective types of knowledge gaps and their lifting.
The category titled robustness of prediction quality demonstrates a lack of relevance across the majority of the selected sources. Only a partial analysis of this aspect is provided by [62] . Nevertheless, a comprehensive investigation is discernible in sources such as [49] and [63] . However, it is important to note that the focus of these investigations lies not in the robustness of artificial intelligence, but rather in assessing the reliability of the mechatronic system itself. While the robustness of AI models is extensively covered in the literature, like in [64] [65] and [41] , it consistently maintains a focal point on artificial intelligence. Consequently, these sources were excluded from the present study.
A closer look reveals in [63] that “one problem in evaluating the reliability of mechatronic systems is that models for evaluating software reliability must first be determined on the basis of extensive development projects that have already been carried out or on the basis of data from testing software that has already been developed. The former is rarely available due to no or poor documentation, and the latter is not available in early development phases.” [ein Problem bei der Bewertung der Zuverlässigkeit mechatronischer Systeme ist, dass Modelle für die Bewertung der Software-Zuverlässigkeit erst anhand von umfangreichen bereits durchgeführten Entwicklungsprojekten oder anhand von Daten aus dem Test bereits entwickelter Software bestimmt werden müssen. Ersteres ist aufgrund keiner oder mangelhafter Dokumentation nur selten vorhanden und letzteres ist in frühen Entwicklungsphasen nicht gegeben]. It is precisely this point that underscores the usefulness of a robust artificial intelligence that can effectively implement precisely this processing and provision of previous knowledge. The methodology offered in [63] is the comparison of solution variants with each other with regard to the achievability of a given reliability target.
When the consideration of optimization proposals with AI is examined, it becomes evident that this aspect also garners significant attention. For instance, [66] and [61] explore the topic to a certain extent, while [58] and [56] provide a more comprehensive analysis. Moreover, a comprehensive examination of this aspect is also found in a broader selection of sources, including [17] and [67] . These sources explicitly emphasize the potential interactions between mechatronics and artificial intelligence, projecting future scenarios, as well as highlighting associated opportunities and risks.
As examples, [67] cites the points of increased efficiency and improved quality, among others. “AI-powered mechatronic systems can optimize production processes, reduce cycle times, minimize energy consumption, and increase overall operational efficiency.” And further, “AI techniques enable intelligent quality control by detecting defects, identifying patterns, and making predictive assessments.” Since there are various AI techniques that can be used in mechatronic product development, the paper proposes a system that takes them into account and subsequently provides an integration-based collaboration approach to artificial intelligence techniques. This system “provides a roadmap for integrating AI techniques into mechatronic systems, paving the way for the future of smart manufacturing.”
The application and substantiation of the concepts and methods can be found across a multitude of sources, although not uniformly. It should be noted that the absence of such substantiation does not necessarily represent a sign of quality, as there may be instances where validation is impractical or unfeasible, for example [68] and [69] . However, particularly detailed proofs of concept can be found in sources such as [28] [54] and [63] , where comprehensive demonstrations of the proposed concepts and methodologies are provided.
In summary, the analysis of the selected sources reveals that while the predetermined aspects are addressed to varying extents, no single paper covers all the categories comprehensively. The holistic cycle and domain linking receive considerable attention, whereas the replacement for human expert knowledge and differentiation from non-relevant knowledge exhibit a more nuanced exploration. Knowledge gaps and the robustness of prediction quality are areas that require further investigation. Optimization proposals through AI garner significant focus, and the application of concepts and methods is evident throughout the literature, albeit not uniformly in all sources.
6. Discussion and Verdict
In conclusion, the integration of AI in mechatronic product development brings numerous advantages, as evidenced by the resources examined in various ways. It is noticeable that actually in all cases only the consideration of individual phenomena or however a group of these is made, a comprehensive consideration of all characteristics presented here is not found—whereby surely also still other points exist. Nevertheless, the various sources make it clear that the resulting benefits are clear and thus each aspect can deliver or is already delivering its corresponding added value for mechatronic product development.
One significant and confirmed advantage is the ability to facilitate the linking of increasingly diverse domains. Mechatronics, by its very nature, encompasses multiple disciplines such as mechanics, electronics, and computer science. The integration of AI allows for seamless integration and interoperability among these domains, enabling a more comprehensive and holistic approach to product development.
Another proven advantage is the capability of AI to complement or even replace human expert knowledge. By leveraging advanced machine learning algorithms and sophisticated data processing techniques, AI systems can analyze vast amounts of data and extract valuable insights. This not only reduces reliance on human experts but also enhances the accuracy and efficiency of decision-making processes in mechatronic product development.
Furthermore, the integration of AI enhances prediction quality. AI algorithms can learn from historical data, identify patterns, and make accurate predictions about system behavior and performance. This predictive capability enables mechatronic engineers to anticipate potential issues, optimize system parameters, and improve overall product performance—in many cases without any kind of new simulations or other experiments.
The consideration of the holistic development cycle is another aspect where AI proves beneficial. AI-based systems can analyze the entire product development cycle, from conceptualization to design, manufacturing, and maintenance. By considering the holistic cycle, engineers can identify potential bottlenecks, optimize processes, and ensure a more seamless and efficient development journey. AI subsequently provides support along the entire process path, through the constant provision of knowledge. At the same time, it is important that there is always a sense of whether this information is reliable or only a rough estimate, which can, however, offer considerable added value in early development phases.
Moreover, AI provides optimization proposals for mechatronic systems. Through sophisticated algorithms, AI can identify areas for improvement, optimize system parameters, and suggest design modifications. This enables engineers to enhance system performance, increase efficiency, and achieve better overall outcomes.
Another advantage lies in AI’s ability to differentiate relevant knowledge. In complex mechatronic systems, not all information is equally relevant or useful. AI can analyze and filter through vast amounts of data, extracting the most pertinent knowledge and discarding irrelevant information. This ensures that engineers focus on the most critical aspects, leading to more efficient decision-making and resource allocation.
Complementary, especially with reference to the previous point, AI helps to address knowledge gaps. In the field of mechatronics, there is often a need to bridge gaps in knowledge and understanding. AI systems can leverage existing knowledge repositories, perform advanced searches, and provide relevant information to fill these gaps. This empowers engineers with comprehensive insights and promotes continuous learning and improvement.
By harnessing the power of AI, mechatronic engineers can make more informed decisions, improve system performance, and accelerate the development of innovative and robust mechatronic products. The ability of AI to link diverse domains, replace human expertise, enhance prediction quality, consider the holistic development cycle, offer optimization proposals, differentiate relevant knowledge, and address knowledge gaps is transforming the field of mechatronics, driving advancements and pushing the boundaries of what is possible. This integration of AI paves the way for the creation of intelligent, efficient, and cutting-edge mechatronic systems that meet the demands of modern industries and societies.