Compression Strength Analysis of Customized Shoe Insole with Different Infill Patterns Using 3D Printing ()

1. Introduction
Additive manufacturing (AM) is the process by which a three-dimensional (3D) object is built up by superimposing material layers using different manufacturing techniques. Although additive manufacturing started in 1987, it has gained momentum over recent years. The advances in technology and cost reduction allow very complex objects to be manufactured in a short time and at an affordable cost [1].
Nowadays, the use of additive manufacturing and 3D printers are very popular [2]. They have a wide range of usage in various industries, including aerospace [3], automotive [4], and construction [5]. At present, 3D printing technology reached shoe manufacturing industries, and high-performance shoes are easier to manufacture with this technology [6]. This technology allows shoe manufacturers to enter the market quickly by experimenting with new designs and providing great customization options. Despite these advantages, the application of 3D printing in footwear is still limited because the technology has yet to provide mass customization. The current study demonstrates a method for increasing the efficiency of shoe insoles in various uses tailored by 3D printing.
Shoe manufacturing companies have been shifting away from leather to almost polymeric shoes. Among these polymers, Thermoplastic Polyurethane (TPU) is a soft material that is highly resistant to wear and abrasion. It is already utilized widely in numerous industries, including footwear. The visco-hyper-elastic property of TPU is preferred due to its elastic property and resistance when subjected to compression [7]. This report focuses on additive manufacturing by a material extrusion process called Fused Deposition Modeling (FDM) 3D printing. The reason for choosing FDM 3D printing is the low-cost equipment and easy processing [8], which makes it suitable to use in small industries. There are many advantages of using FDM 3D printing compared to the conventional manufacturing process because the conventional process cannot change the internal infills of the shoe insole [9]. With the use of slicer application, numerous infills can be applied to the insoles. In this study, shoe insoles were designed with the help of the software known as Gensole [10], which is used to design customized insoles. This design is suitable for all types of foot problems, as shown in Figure 1.
There are different types of foot problems [11]. Some of them are flat feet, high arch, and very high arch. If the shoe insole is designed according to individual
![]()
Figure 1. Different types of feet problems.
foot parameters, then they will be more comfortable for the users. In Gensole, the shoe insole can be modified by inserting the STL file of the leg on the insole. In this study STL file of the leg is prepared with the help of the polycam application, and it can be available on mobile phones.
2. Materials and Methods
2.1. Material
Thermoplastic polyurethane (TPU) is a promising polymer with a wide range of practical applications. It was demonstrated that the 3D printing of TPU provides a unique possibility to manufacture customizable, flexible structures that can be designed and optimized for specific energy absorbing applications [12].
TPU is generally a 3D printing material. Its linear polymer chains make it in the form of wire, with flexible and rigid chains connected through covalent bonding. Therefore, it displays flexibility, elasticity, and shock resistance like rubber and thermoplastic. This study used PolyFlex TPU 90 A with a diameter of 1.75 mm, as shown in Figure 2. Because of its properties which are suitable to produce the shoe insole.
2.2. Properties of TPU
Generally, TPU has a high elongation and tensile strength. Compared with other rubber-like elastic materials, TPU has an excellent compressive strength. Like ordinary thermoplastic, they can be used in injection, blow, and compression moulding applications. These elastomers have low-temperature flexibility. It has excellent abrasion and tear resistance and high hardness [13]. In addition, they are highly resistant to ozone, aliphatic solvents, and petroleum-based fuels and oils.
2.3. Additive Manufacturing
Additive manufacturing refers to a group of technologies that can quickly and
easily convert virtual solid model data into physical models by adding material. AM will make benefit in many ways. The manufacturing process can be carried out straight from the 3D design, eliminating the need for any intermediate process or tooling, such as the usage of injection moulds. This process shortens the production cycle and enables design teams to create high-quality prototypes in a matter of hours [14]. It also makes it easier to produce small-batch series or customized products, such as insoles. The unique capability of AM includes shape complexity which is easy to produce virtually any shape by avoiding the approximations imposed by the machining process [15].
2.4. Fused Deposition Modelling (FDM)
3D printing using Fused Deposition Modelling (FDM) is one of the most used additive manufacturing techniques [16] [17]. These printers can produce items by heating and extruding a thermoplastic filament that deposits layer upon layer. The widespread usage of this system has been recently boosted by the expiration of the FDM patent and the subsequent worldwide development of low-cost machines by a huge number of companies [18].
The FDM-printer used in this study is a “Creality ender 3V2” shown in Figure 3. It is equipped with a carborundum glass platform. This platform enables the build plate to be heated up quickly, and the molten filaments to adhere to the build plate well without warping. The printing size of this 3D printer is 220 × 220 × 250 mm, and the main advantage of this FDM 3D printer is that it is user-friendly [19].
2.5. Slicer (Prusa)
Slicing is one of the main steps in FDM where 3D CAD model is virtually converted into layers and then G-codes. The quality of the sample is based upon the layer height. To achieve the smoothest walls, a fine print setting of 0.12-mm layers
![]()
Figure 3. “Creality ender 3V2” 3D printer.
[20] were used in this study, perimeter as “1”, top and bottom layers were taken as “0”. According to the compressive strength, different infill patterns were taken at different regions of the insole, as shown in Figure 4.
2.6. Infill Pattern
In this study, four infill patterns (A-Triangle, B-Rectilinear, C-Gyroid, and D-Cubic) were used, as shown in Figure 5. Generally, the higher the infill percentage, the higher the object’s strength. According to the requirement, an infill percentage should be chosen. This study focuses on three infill percentages (25%, 40%, and 60%) used at different insole locations. Infill has various factors in the slicer. Among those factors, fill patterns, fill density, and fill angle are very important.
2.7. Parametric Design of Shoe Insole (Gensole)
In this study, the design of the insole was taken from the “Gensole Software”. In Gensole, modification of the shoe insole is easy. By just dragging the points, modification can be done. Height, length, and width of the insole can be modified easily according to the size of the leg. These insoles are generally for the person with all type of feet. Some people have problems (flat feet, high arch, and very high arch) with the foot’s shape. This insole can be modified easily by placing
![]()
Figure 4. Different infill patterns at various regions.
the STL file of the leg on the insole. After inserting the leg file on the insole, the pressure of the foot can be seen in the form of colors (red, orange, and yellow). This can be seen in Figure 6. The red color indicates more pressure, and this
![]()
Figure 5. Infill patterns ((A) Triangle, (B) Rectilinear, (C) Gyroid and (D) Cubic).
![]()
Figure 6. Modifications of the insole after placing the leg file.
region can be divided into parts as shown in Figure 4. The infill patterns and infill percentages in this region can be decided with the better compressive strengths which can be taken from the compressive test. Table 1 shows the specifications of the insole before and after the placement of the STL file leg.
2.8. Compression Test
Compressive testing demonstrates how a material will react when compressed. Compression testing can identify a material’s behaviour or response under crushing loads and evaluate its plastic flow behaviour and ductile fracture limits [21] [22]. Compression tests are important for determining brittle or low-ductility materials’ elastic and compressive fracture properties.
Compression tests are also used to determine the modulus of elasticity, the proportional limit, the compressive yield point, the compressive yield strength, and the compressive strength. These qualities are vital in determining whether a material is suitable for a particular application or fails under specific stresses. Compression tests were done on the Universal Testing Machine (UTM) from Zwick. The following compression tests were conducted according to DIN ISO 604.
3. Results and Discussions
3.1. Compression Modulus vs Weight
Here, with high compression modulus values infill percentages were selected as compared with the weight.
60% Infill
A standard cylindrical specimen of 20 mm diameter and 30 mm height was taken. First, 60% infill was used for the test and then compared among four infill patterns. Triangle and rectilinear have better results when compared to other patterns. (Graph 1)
![]()
Table 1. Specifications of the insole before and after inserting leg file.
40% Infill
Now, 40% infill was used for the test and compared all the patterns. Gyroid and triangle infill patterns have better results when compared to other patterns. (Graph 2)
25% Infill
For 25% infill density, gyroid and triangle infill patterns showed better properties in terms of compressive modulus and weight. (Graph 3)
3.2. Compressive Strength vs Compressive Strain
Here, with high compression strength values infill patterns were chosen as compared
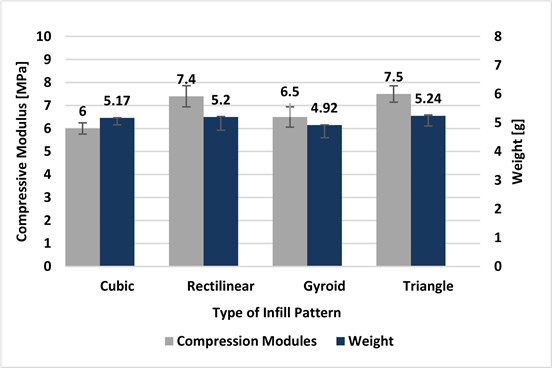
Graph 1. Comparison of compressive modulus of different patterns with 60% infill.
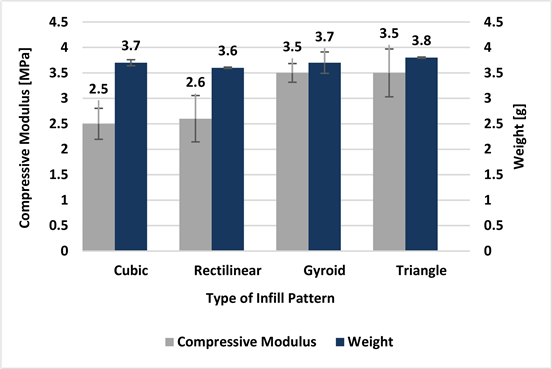
Graph 2. Comparison of compressive modulus of different patterns with 40% infill.
with compression strain.
60% Infill
A standard cylindrical specimen with a diameter of 20 mm and a height of 30 mm was used. In this case, 60% infill was utilized for the test and compared with all the patterns. Rectilinear and triangle infill patterns gave better results. (Graph 4).
40% Infill
Here, 40% infill was used for the test and then compared among four infill patterns. Comparing all the patterns, triangle and rectilinear were best with this infill. (Graph 5)
25% Infill
In this test, all patterns were compared using a 25% infill. Finally, with this infill,
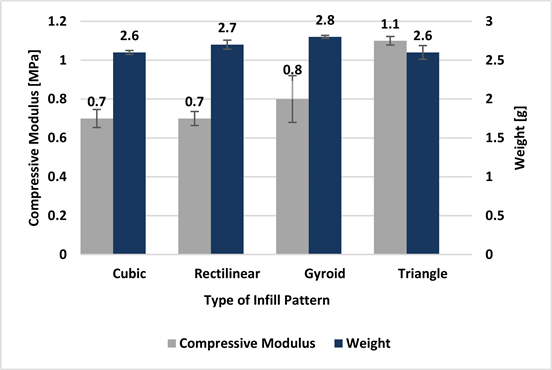
Graph 3. Comparison of compressive modulus of different patterns with 25% infill.
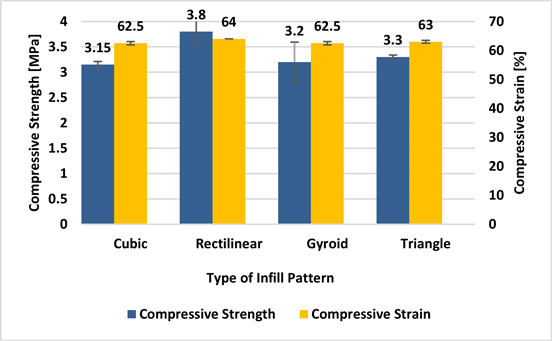
Graph 4. Comparison of compressive strength and compressive strain with 60% infill.
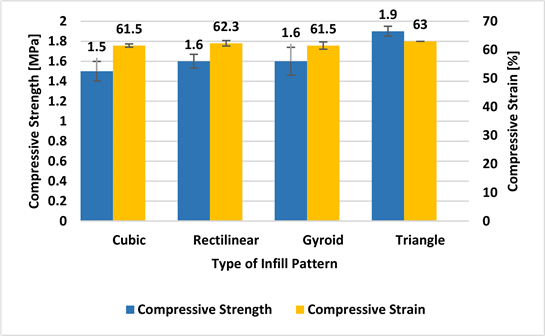
Graph 5. Comparison of compressive strength and compressive strain with 40% infill.
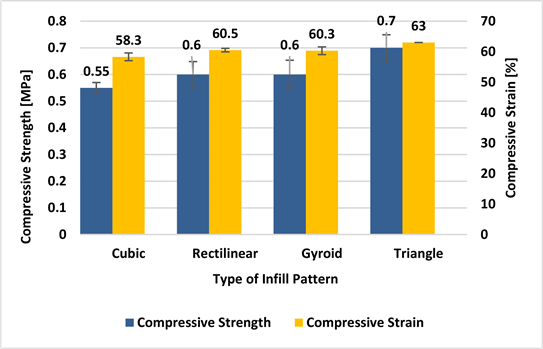
Graph 6. Comparison of compressive strength and compressive strain with 25% infill.
triangle, gyroid, and rectilinear were the best among all the patterns. (Graph 6)
4. Conclusions
This research aims to analyze the compression strength of a customized shoe insole by using different infill patterns. Using PolyFlex TPU material, a compression test was performed to determine compressive modulus and strength. The triangle, the rectilinear, and the gyroid patterns got better results in this report. However, the cubic pattern was eliminated due to its low compressive strength. Implementing a combination of different infill patterns and infill percentages in a single insole can further reduce the usage of material, which results in cost-effectiveness. The advanced features in the Prusa slicer have helped to produce several regions in the single insole. These resulted in using different infill patterns in a single insole. Most shoe companies are producing shoe insoles with only one infill pattern and infill percentage which results in consuming more material. Another important software used in the research was Gensole. This software produces the shoe insole with weight as input. After inserting the STL file of the leg in the insole, modifications can be done. These modifications of the insole are easy by just dragging the points according to the size of the foot. These insoles can also be used by people who have foot problems.
This study proved that 3D printing is effective in making an insole that responds to the requirements of different individuals based on the infill patterns design. By using Carborundum Glass Platform as a build surface in FDM 3D printer, the prints adhere better to the bed without warping. This research brings innovation into customized 3D-printed shoe industries by providing these meaningful insights into the design process. The models with different thicknesses and materials were not considered here. The focus was exclusively on the interior pattern of 3D-printed insoles that deliver various functionalities.
This study also provides the scope of using a combination of patterns in a single insole and provides more support and comfort as per an individual’s requirements.
Acknowledgements
The authors acknowledge that this study is supported by Prof. Jens Schuster for providing laboratory equipment and its facilities at University of Applied Sciences Kaiserslautern, Germany & Institut für Kunststofftechnik Westpfalz (IKW).