Combine Harvester: Small Machine Solves Big Rice Harvesting Problem of Bangladesh ()
1. Introduction
The global population will reach 9.61 billion by 2050 and 11.2 billion in 2100 [1]. Consequently, the staple food consumption, comprising wheat, maize and rice is likely to increase vividly, especially in developing countries [2]. More than double food and production are required to ensure global food security [3]. This situation is challenged by expected pressure on global cropland availability. As a result, worldwide calls intensify production on available land sustainably (to keep natural land conservation, avoid biodiversity loss) [3]. These problems are acute in densely populated South Asian countries, including Bangladesh, which records a poor population living less than USD 1.90 day−1 [4]. In Bangladesh, almost 38.85% of the population depended primarily on agriculture [5], and about 87% of rural households income depended on agriculture [6]. The country’s agriculture sector also contributes approximately 13.68% of the country’s gross domestic product (GDP) [6] and employs more than 45% of the total labor force [7]. To keep the food supply pace with the additional two million population added annually, Bangladesh will need to increase rice and wheat production by 0.4% and 2.17% per year, respectively [8]. Moreover, the most recent studies [9] [10] estimated that feeding 215.4 million people in 2050 will be required 44.6 million tons of cleaned rice, whereas annual land shrinkage is 0.08 million hectares due to non-agricultural activities.
In Bangladesh, rice is an important cereal crop for national food security and is estimated for 93% of all food produced [11]. Also, 70% of calorie intake is from rice [12]. [13] noted that “rice security” is synonymous with “food security” in Bangladesh, like many other rice-growing nations. Therefore, satisfactory rice production is the primary strategy to ensure Bangladesh food security [10]. Accordingly, the Government of Bangladesh has prioritized increasing the main cereal crop (rice), contributing to socio-economic development. Furthermore, Bangladesh’s people called: rice is a political crop, because government stability depends on rice availability. The primary way to increase rice production is: 1) yield intensification, 2) yield gap minimization between the research field and farmer’s level, and 3) postharvest loss reduction. Several research results noted that mechanical intervention is one of the best ways to decrease the yield gap, minimize the postharvest losses, increase the farmers’ revenue [12] [14] [15].
Rice production depends on land cultivation, planting, intercultural care, harvesting and processing [16]. Among the crop production actions, harvesting is a decisive activity regardless of all crops, related to productivity and farmer’s income [10]. Rice harvesting system belongs to cutting, transportation, threshing, cleaning and bagging (Figure 1). In developed countries, most of the harvesting action is done mechanically, but in developing countries, harvesting mechanization is partial due to lake of sustainable technology and machinery use knowledge gap (Figure 2). For example, in Bangladesh, 95% of cutting is done manually (sickle), but 95% of threshing was completed by machine [17].
![]()
Figure 1. Flow diagram of present harvesting system in Bangladesh.
![]()
Figure 2. Schematic diagram of mechanization.
However, manual harvesting, mostly cutting and transportation associated with struggle, laborious, costly and huge postharvest losses.
On the other hand, mechanized harvesting offers farmers various benefits as 1) less cost per unit; 2) timely harvesting; 3) keep on both quality and quantity; 4) contribute to expanding total productivity; and 5) provide a sustainable, cost-effective transition of the labor pool (Figure 3). As a result, harvest mechanization has received considerable attention globally, to the farmers, researchers, policymakers due to its substantial beneficial consequence. Also, individual farmers, co-operatives, and government stakeholders have used various harvesting technology to make profitable agricultural (Table 1). Moreover, public and private organization are likely to research and develop machinery suitable for Bangladesh conditions (Table 2). Nevertheless, Bangladesh perspective has no sufficient information on harvest mechanization. Therefore, the present study’s primary objectives are to bring detailed information on combine harvester use that involves harvesting cost, economic outturns, machinery efficiency, etc.
In addition, farmers in developing and developed nations are terrified about the technological performance of farm machinery. Hence, the adoption rate of
![]()
Table 1. Harvesting machinery available and area coverage in Bangladesh.
![]()
Table 2. Research organization and developed technology for paddy harvesting in Bangladesh.
technology is prolonged in most Asian countries, like Bangladesh. However, as the combine harvester is modern technology, the farmers of Bangladesh are not updated about use and handling. Moreover, the farmers are poor, so they have no capital to purchase the machine. Also, farmers have no idea about the benefits of combine harvester. Therefore, the above reasons are the main point of lack behind mechanization.
![]()
Figure 3. Outline of harvesting mechanization benefits (Adopted from [25] ).
Last decade, the farmers and policy levels increasingly adopted the machinery used frequently. However, there is very little up-to-date information regarding harvesting machinery such as reaper, thresher, winnower, bagging system, and overall combine harvester in Bangladesh. Also, harvesting machinery sustainability rates are low; still, the reason is unknown. [25] mentions that the government’s knowledge gap and economic support were the main reasons for the low adoption rate of machinery in Bangladesh. [26] also noted that appropriate farm machinery adoption could be an essential policy and development goal of Bangladesh. The Government of Bangladesh has recently prioritized harvesting mechanization for food availability [27]. However, many vital aspects of combine harvester’s as labor required to harvest unit area, harvesting losses, feasibility with Bangladesh land perspectives are poorly understood, so comprehensive harvesting mechanization is not well documented. The adoption of ultimate harvesting machinery (combine harvester) needs detailed information like human drudgery, cropping intensity, crop productivity, etc. Also, a machine’s technical and economic performance is required to conclude the benefit. Therefore, the study was undertaken to gather specific information on harvest mechanization by combining harvester in Bangladesh.
2. Research Project and Methodology
2.1. Range of Data Arrangement
The field experiment was conducted in the Gazipur district, Bangladesh, to determine harvesting machinery’s work efficiency in Boro 2016 to 2018 season (April-May). The study focused on operation cost, labour-saving and work efficiency for mechanized, semi-mechanized and traditional practice. Research undertook commonly practised actions and machinery to cut, transport, thresh, and clean paddy.
2.2. Field Operation Techniques
Many variations in the farmers’ harvesting, threshing, and cleaning practices. Therefore, the following three methods, combined with traditional and modern harvesting, threshing and cleaning, were evaluated to determine work efficiency and economics (Table 3).
2.3. Procedure to Determine the Work Efficiency
This study explored the work efficiency, economic analysis and postharvest loss methods from a book chapter by [28]. Method 1 (T1) incorporated with paddy cutting by sickle, transported the harvested paddy by head or shoulder, threshed the paddy by beating and finally cleaned by Kula. Alternatively, reaper for paddy harvesting, trolly for harvested paddy transportation, close drum thresher for threshing and winnower for cleaning was considered for method 2 (T2). Both the T1 and T2, binding techniques were the same pattern (manually). Process (T3) was fully mechanized vis-a-vis using a combine harvester. The performance indicating methods are:
Method, T1: Sickle + Head carry + beating + Kula
Method, T2: Reaper + Trolly carry + Close drum thresher + winnower
Method, T3: Combine harvester
The machine’s efficiency is defined as the device’s useful work to the actual work. This activity included beating, close drum thresher, winnower and combine harvester. The field size or sample size was necessarily large to ensure greater accuracy. Before the final test, a pre-test was arranged to minimize the error and adjusted. Box 1 depicts the work efficiency test activity for performance indicating methods (T1, T2 and T3). Undertook some empirical equations for calculating work efficiency, economic analysis and postharvest losses.
2.4. Selection of Machinery
Machinery and equipment selection is vital in obtaining reliable and accurate field results. The assorted machinery is listed in Table 4 to conduct the field experiment. The central machinery is Korean made head feed combine harvester.
![]()
Table 4. Listed machinery/activity and main specifications.
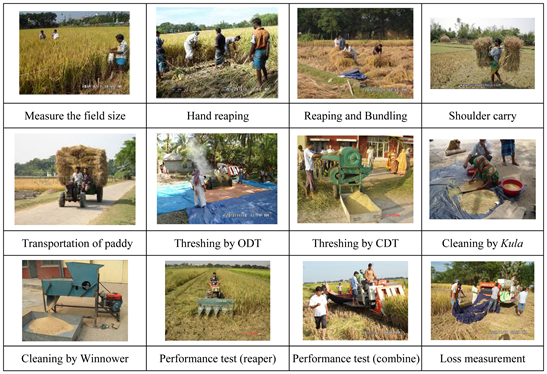
Box 1. Pictorial view of work efficiency test activity.
2.5. Performance Parameter
The performance factors are listed to evaluate a combine harvester’s technical and economic efficiency during paddy harvesting and compare with other harvesting systems. The performance elements were: 1) labor per unit area, 2) field capacity, 3) field efficiency, 4) operational time, 5) operating cost and 6) grain losses.
2.5.1. Work Efficiency Calculation
Field efficiency/work efficiency is the ratio between a machine’s productivity under field conditions and the theoretical maximum productivity. Field efficiency accounts for failure to utilize the machine’s theoretical operating width; time lost because of operator capability and habits and operating policy; and field characteristics. The calculation did not include travel to and from a field, significant repairs, preventive maintenance, and daily service activities for field time or efficiency. Field efficiency is not a constant for a particular machine but varies with the field’s size, shape and pattern, crop yield, moisture, and crop conditions. This study used the following formula to calculate work efficiency.
Labor per unit area
(1)
where,
MPA: labor per unit area, man-h∙ha−1
TW: working time for harvesting process, min
PW: working person, m
AW: working area for harvesting process ha)
Theoretical field capacity
(2)
where,
Cth: Theoretical field capacity, ha∙h−1
W: Theoretical working width, m
V: Theoretical working speed of the machine, m∙s−1
Theoretical operation time
(3)
where,
Tth: Theoretical operation time, min
A: Area of a plot, ha
W: Theoretical working width, m
V: Theoretical working speed of the machine, m∙s−1
Actual field capacity and efficiency
Actual field capacity and efficiency
(4)
(5)
where,
C: Field capacity, ha∙h−1
A: Area of a plot, ha
T: Field operation time
Ef: Field efficiency
Cth: Theoretical field capacity, ha∙h−1
Area coverage
(6)
where,
H: Coverage, ha
εu: Network hour rate
εd: Available working day rate
C: Field capacity, ha∙h−1
U: Daily operation time, h
D: Duration of operation, day
N: Number of operations
Turns number
(7)
(8)
(9)
(10)
where,
n180: Number of 180 degree turns
Nsy: Number of run-strokes alongside the long side
Nc: Number of circuitous turns
n90: Number of 90 degree turns
lm: Length of machine, m
w: Effective working width, m
x: Width of unit field, m
Operation time
(11)
where,
T: Field operation time, min
Te: Total time requirement for operation, min
Tloss: Loss time, min
Tturn: Turning time, min
Tidle: Idle travel time, min
Tpf: Preliminary or finishing operation time, min
Tio: Time for getting in and out field, min
x: Width of unit field, m
y: Length of unit field, m
v: Working speed of machine, m/s
w: Effective working width, m
Time calculation
(12)
(13)
(14)
where,
Tturn: Turning time, min
n180: Number of 180 degree turns
t180: Time for a 180 degree turn, s
n90: Number of 90 degree turns
t90: Time for a 90 degree turn, s
Tidle: Idle travel time, min
y: Length of unit field, m
v: Working speed of machine, m∙s−1
Tpf: Preliminary or finishing operation time, min
x: Width of unit field, m
Tio: Time for getting in and out of field, min = 5
2.5.2. Economic Analysis
Economic analysis is obligatory for concluding any technology is viable, suitable and fit for farmers. The study’s main objective is to derive the benefit and cost of rice combine harvester investment and its economic returns by applying the basic concept of an analysis of investment returns.
Operating cost
(15)
(16)
where,
YC: Annual operating cost, Tk∙yr−1
FC: Annual fixed cost, Tk∙yr−1
YVC: Annual variable cost, Tk∙yr−1
DP0: Depreciation cost, Tk∙yr−1
RC: Annual repair cost, Tk∙yr−1
Fixed cost
(17)
(18)
where,
DPO: Depreciation by straight-line method, Tk∙yr−1
P: Purchase price, Tk
S: Salvage value, Tk
n: Service life in years
RC: Annual repair cost, Tk∙yr−1
yrf: Annual repair cost factor, 0.05
Variable cost
(19)
(20)
(21)
(22)
where,
YVC: Annual variable cost, Tk∙yr−1
UHR: Yearly available working time, h∙yr−1
FOH: Fuel and oil cost per hour, Tk∙h−1
LH: Labor cost per hour, Tk∙h −1
FUP: Fuel price, TK∙l−1
FUR: Fuel consumption per hour, l∙h−1
OFR: The ratio of oil and fuel cost
WAG: Wage per hour, Tk∙h−1
NOP: Number of operators
NAU: Number of auxiliary operators
AR: Area of machine management, ha∙yr−1
C: Field capacity, ha h−1
2.5.3. Postharvest Losses
In the experiment, for harvesting losses measurement, considered the following formula. Generally, there are three types of losses for combine harvester (shatter/cutter bar loss, cylinder/threshing loss and separating/cleaning loss). However, the losses are five types in a traditional system (Shattering/cutting loss, bundling loss, transportation loss, threshing loss and cleaning loss).
(23)
(24)
where M0 = Initial Moisture
(25)
(26)
(27)
(28)
(29)
(30)
(31)
2.5.4. Technique of Simulation
Simulation and calculation are integral parts of analysis. For forecasting, actual condition simulation is necessary. Sometimes the simulation value is higher or lower, thus showing the actual condition. Simultaneously improved and developed by simulation are required to achieve the fundamental components quickly. For getting the accurate information of combine harvester, here simulation was considered.
3. Results and Discussion
3.1. Work Efficiency
Work efficiency is a significant factor to evaluate the technology. The total workforce requirement of T1 (278.0 man-h∙ha−1) was comparatively higher than T2 (238.1 man-h∙ha−1) (Table 5). The reaping and transportation capacity was a difference in T1 and T2. The reaping capability depends on planting intensity, the cutting plant’s height, and labor skill. A hand beating capacity is lower than a close drum thresher, so the labor requirement for threshing is in an inverse relationship. On the other hand, the paddy comes clean in a closed drum thresher because most threshers have cleaning facilities.
Table 6 expresses the combine and actual/simulation with field test (analysis) working efficiency. Here, the working width and theoretical field capacity are the same, but the total working time is different. The analysis result is higher than the combine test result because the analysis considered the machine’s time to enter and leave the field. So, the actual (analysis result) field efficiency, field capacity and coverage were higher than the combine harvester’s work. The combined labour requirement (6.37 man-h∙ha−1) was lower than the analysis result (9.87 man-h∙ha−1).
![]()
Table 5. Working capacity analysis.
![]()
Table 6. Working efficiency of the combine harvester.
3.2. Comparison of Labor Requirement per Unit Area/Labor Saved
Labor involvement during paddy harvesting is a vital factor in harvesting costs. Table 7 compares the labor required for T1, T2 and T3. Here, T1 requires 28.67 times more labor and T2 requires 15.6 times more labor than combine harvester. [29] notices that rice manual harvesting is a laborious, time-consuming and
![]()
Table 7. Comparison of labor requirement (man-h/ha).
costly operation that requires about 100 - 150 persons to harvest 1 ha of paddy field and was responsible for both quality and quantity losses.
So the use of combine harvester was more effective than traditional reaping, transportation and threshing. The combine harvester does not require bundling, transportation, and winnowing because the reaping, threshing, and cleaning are done simultaneously. Ultimately, combine harvester is the most significant and commercially labor-saving invention and significantly reduces labor requirements in agriculture [30].
3.3. Area Coverage of Combine Harvester
Table 8 shows the coverage calculation for the combine harvester. The plot geometry coverage was 156.11 ha∙yr−1, which was higher than the actual (simulation) coverage of 100.73 ha∙yr−1. However, this result was not correct because the plot size was small. Therefore, the experiment should be carried out in a big field for a better and more reliable result. Here, we consider only two seasons per year. But in some areas, rice is grown three times. So depending on the crop growing region, the area coverage may need to be changed.
3.4. Economic Analysis of Paddy Harvesting Cost
Table 9 compared the operating cost of methods T1, T2 and T3. For traditional practice (T1), all operations during paddy harvesting were cleaned manually. Alternatively, the semi-mechanization process (T2) was done by machine as a reaper for harvesting, bundling by hand, power tiller operated trolley for transportation, close drum thresher for threshing winnower for cleaning (Table 9). Cost calculated according to the needed man-day per hectare. As shown in the table, the harvesting costs were 1.84 (semi-mechanization) and 2.5 (manual) times higher lower than the combine harvester. The like outcome by [31] and research demonstrated that mechanization production cost decreased from 4 to 10-fold (Table 10).
3.5. Cost Calculation
Reducing harvesting costs as a percentage of total production costs is one of mechanization’s main factors. Modern harvesting technologies are already adopted in developing countries to maintain grain quality [10]. Table 11 provides the economic analysis for the combine harvester operation cost calculation. This table also expresses the simulation of combine operating costs. The fixed
![]()
Table 8. Annual area coverage of combine harvester.
![]()
Table 9. Comparison of paddy harvesting cost.
Note: 84.0 Bangladeshi Taka (Tk) = 1 US$; *Paddy carrying; **Straw binding and carrying.
![]()
Table 10. Economic analysis of combine harvester.
Note: *two rice-growing seasons yearly.
![]()
Table 11. Percent loss estimates in rice for the harvesting system.
price was the same in both combine harvester and simulation; however, variable and operating cost differs. A farmer can save 61% of the harvesting cost (Table 11). This is similar to [14] ’s research result and combine harvester could save 52% of harvesting cost compared to hand harvest. A field experiment conducted by [32] showed that 58% and 46% of expenses were saved using a mini-combine harvester and a reaper.
3.6. Postharvest Loss
The postharvest depends on variety, harvesting time (mature/over mature), and natural conditions [10]. Paddy harvesting losses (cutting, bundling, threshing and cleaning) for T1, T2 and T3 were determined during Aman season 2016 and summarized in Table 11. The field experiment was conducted in good weather condition. The weight of grain losses and total yield were encountered for the estimation of losses. Average cutting, bundling, transportation, threshing and cleaning loss for T1 were found 0.49%, 0.44%, 0.21%, 1.54% and 0.40%, respectively. Alternatively, for T2, the total loss was 2.94%, which was less than traditional harvesting T1 (3.09%). [10] and [33] reported that manual harvesting loss is higher than mechanical.
Moreover, the cutting and threshing losses were 0.13% and 1.25% in the combine harvester. In a combine, the cleaning (chaff) loss was negligible. Finally, the combine harvester postharvest losses were 3 to 4 times less than traditional (T1) and semi-mechanized (T2) harvesting systems. As the combine has no transportation loss, they can avoid bundling and transport loss if farmers use a combine, ranging from 0.14% to 0.21%. This result is similar to [32]. They noted that mini-combine and reaper could reduce rice harvesting by 5.12% and 2.14%, respectively, compared to manual harvesting systems. Regarding postharvest issues, the combine harvester used might benefit the farmers.
It is well-known the loss of paddy could be saved using the combine harvester over manual harvesting and a semi-mechanized system. Paddy loss could be held at 1.84% using the combine and 0.15% by the semi-mechanization system (Table 6). [10] [33] [34] reported that grain loss using a combine harvester varies ranging from 1.43% to 5.6%. Similarly, another study conducted by [35] suggested that mechanical harvesting can avoid a 3% postharvest loss per season. Therefore, mechanized harvesting is a justified way to reduce postharvest loss and be more feasible and economical than traditional [36].
4. Conclusions
Bangladesh’s common postharvest practices are harvesting by sickle, field transport on head and shoulder, piling of harvested stalks at the home yard, threshing by hand beating and/or power thresher, and cleaning threshed paddy by winnowing basket (Kula). However, due to colossal government initiatives, mechanical harvesting technology boosts especially harvester popularisation activities. The study showed that less harvesting cost, less labor requirement and low postharvest loss are the primary advantages of a combine harvester. However, even the machine purchasing cost remains beyond the farmer’s capacity. However, both the quality and quantity deterioration of grain due to delayed harvesting and profitability are major concerns of manual harvesting. Therefore, for Bangladesh, combine harvester is smart technology for solving big harvesting problems of Bangladesh.
This work characterized a small combine harvester’s work efficiency, economic analysis, and postharvest loss assessment and compared manual harvesting’s potential impact. However, small-scale combine harvester can benefit Bangladesh’s fragmented crop fields and is considered here and has a considerable benefit over the traditional practice. However, these benefits may not be significant enough to outweigh economic factors associated with capital cost, operational expenses and break-even point. Therefore, a complete techno-economic analysis should be conducted to thoroughly explore a small-scale/large combine harvester’s relative advantages.
Acknowledgements
The authors would like to acknowledge the “Strengthening Farm Machinery Research Activity for Mechanized Rice Cultivation (SFMRA) Project” FMPHT Division, BRRI, Bangladesh, for providing the financial support to publish this research work.
Disclaimer
The views expressed in this article are those of the authors and do not necessarily represent the Bangladesh Government or the authors’ institution and shall not be used for advertising or product endorsement purposes.
Author Contributions
The article is the result of joint work.
Funding
The research did not receive any specific grant from funding agencies in the public, commercial, or not-for-profit sectors.
Supplementary Data
Supplementary data and information to this article can be found online at (https://www.researchgate.net/publication/332670341_Improvement_of_Paddy_Harvesting_Mechanization_System_for_Bangladesh)