1. Introduction
Polypropylene is an important plastic and is used in many different forms and applications through a range of manufacturing processes. A large proportion of polypropylene is used in fibers as constituents of fabrics, upholstery and carpets [1]. Blow moulded containers, such as bottles for foods, shampoos and other liquids, form part of everyday experience. A wide range of injection moulded items exists in appliance housings, resistant containers, car components, toys and furniture [2]. Control of stereospecificity can be achieved by using either a C1 (iso or hemi-isospecific), C2 (isospecific) or a Cs (syndiospecific) catalysts and in our work we used a C2 symmetric catalyst in particular [3]. One of the main advantages of homogeneous polymerization catalysts compared to multisited heterogeneous catalysts is their well defined active sites, which allows us to synthesize polymers with specific microstructures and more narrow molecular weight distributions which are quite uniform. Kaminsky and Sinn’s [6] [7] discovered that a hydrated form of trimethylaluminum, methylaluminoxane (MAO), afforded extremely active catalysts when combined with titanium and zirconium metallocenes led to an explosion of research into the use of metallocene catalysts. Since that finding, several advances have been made in which variation of the zirconocene symmetry and polymerization conditions was found to strongly influence the resulting polyolefin microstructure and polymer properties [8] [9]. The aim of this work was the synthesis of various molecular weight polypropylenes including high molecular weight polypropylene. This was achieved by varying the polymerization conditions such as temperature, pressure, Al/Zr ratio and polymerization time. The structure of the catalyst used was as shown below.
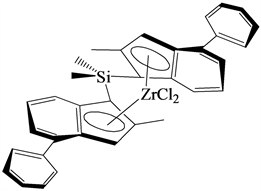
[Me2Si(2-Me-4-Ph-Ind)2]ZrCl2 catalyst system
2. Experimental
2.1. Materials
All operations were performed under nitrogen gas using standard Schlenk techniques and all solvents were purified by a solvent purification system. Research grade propylene (PS-MD-5) and nitrogen were obtained from Shanghai Wei Chuang standard gas company was purified by passing it through dehydration column of ZHD-20 and deoxidation column of ZHD-20A. The metallocene ([Me2Si(2-Me-4-Ph-Ind)2]ZrCl2) was obtained from boulder scientific company and was used as received. Ethanol, HCl and Toluene were obtained from Shanghai Ling Feng Company. MMAO (modified methyl aluminoxane) was obtained from Wuhan methyl technology limited company. BHT was obtained from J&K Company.
2.2. Polymerization Procedure
To a 100-ml single-neck round bottom glass flask having a magnetic stirrer was added certain amounts of toluene, MMAO and BHT. Using a vacuum, the solution was degassed and gaseous propylene was added to the mixture, all the procedures taking place at room temperature. Afterwards, the solution was saturated by propylene at 1 atm.
Polymerization was initiated by addition of zirconocene catalyst/toluene solution and was continued by maintaining the atmospheric pressure and ensuring a continuous propylene feed. The polymerization was terminated by addition of drops of ethanol solution at first and then the reactants were poured into dilute HCl/ethanol solution. The precipitated polymers were filtered and the filtered polymers were then dried under vacuum at 60˚C for 6 hrs.
2.3. Polymer Characterization
Molecular weights number average (Mn) and molecular weight distributions (Mw/Mn) of the polymers were measured using a PL GPC-220 with a DRI detector at 150˚C using 1, 2, 4 trichlorobenzene as the solvent. The calibration was done by Polymer Laboratories detector software Cirrus with PS (Polystyrene) standard. The analysis for PP (Polypropylene) was conducted using the parameter of Mark-Houwink equation (K = 1.0 × 10−4, α = 0.74 for PP, cf. K = 1.4 × 10−4, α = 0.70 for PS).
3. Results and Discussion
3.1. Effect of Al/Zr Mole Ratio
Generally, with metallocene catalysts, the activity of polymerization increases with the Al/Zr mole ratio increase and reaches a maximum value at a particular mole ratio. If the mole ratio is increased beyond this point, the activity usually remains constant, or decreases slightly [4]. The effect of the Al/Zr mole ratio on the propylene polymerization rate was studied by varying the Al/Zr ratio from 1000 to 4000. As Figure 1 and Table 1 clearly shows, the propylene polymerization rate was low when the Al/Zr mole ratio was 1000. When the concentration of Al/Zr was increased, the activity rose rapidly until Al/Zr mole ratio of 3000 had been reached. With higher Al/Zr ratio of 4000 a slight decrease was observed. This was true at both 0˚C and 25˚C. As Figure 2 clearly shows, the molecular weight was low when the Al/Zr mole ratio was 1000. When the concentration of Al/Zr was increased, the molecular weight increased until a Al/Zr mole ratio of 3000 had been reached. With higher Al/Zr ratio of 4000 a slight decrease was observed. However at 40˚C the activity reduced with increasing mole ratio and this could be due to the fact that the higher temperature led to chain transfers which in turn lowered the activity and rate of polymerization [5]. The molecular weight also followed the trend of the activity at 40˚C and reduced as the Al/Zr ratio increased. The molecular weight distributions in all cases did not follow a pattern in particular but were close to 2 to signify the samples obtained were homogenous in nature.
3.2. Effect of Polymerization Temperature
The effect of polymerization temperature was investigated changing the polymerization temperature three times. The activity of the catalyst was heavily dependent on the polymerization temperature, as depicted in Figure 3 and Table 2. Polymerization activity was low at 0˚C and increased at 25˚C and was highest at 40˚C. The molecular weight was also dependent on the polymerization temperature and was highest at 0˚C, reduced at 25˚C and was lowest at 40˚C. The reason for this could be that as the temperature increases, the chain transfer reactions increase and this has an overall effect of lowering the molecular weight.
3.3. Effect of Polymerization Time
The effect of polymerization time was investigated by changing the polymerization times at the same polymerization conditions, i.e. same Al/Zr ratio and temperature. The following runs were compared as they had the same polymerization conditions but varying polymerization times. (Run 2 and 12, run 13 and 14, run 15 and 16, run 17, 18, and 19). The activity of the catalyst was heavily dependent on the polymerization time, as depicted in Figure 4 and Table 3.
Comparing run 2 and 5, the activity increased with increase in polymerization time at 25˚C. Consequently, the molecular weight was also dependent on the polymerization time at this temperature and the molecular weight increased when the time was increased from 7 to 10 minutes since more monomers were added to the growing chain and this led to an increase in the molecular weight.
![]()
Table 1. Table showing homopolymerization results of propylene at different Al/Zr ratioa.
aPolymerization conditions: Solvent = Toluene, total volume 50 ml, Zr = 5 µml, bActivity in kg-polymer/mol Zr.hr, cNumber average molecular weight and molecular weight distribution determined by GPC using polystyrene standard.
![]()
Table 2. Table showing homopolymerization results of propylene at different temperaturea.
aPolymerization conditions: Solvent = Toluene, total volume 50ml, Zr = 5 µml, bActivity in kg-polymer/mol Zr.hr, Al/Zr ratio = 2000; cNumber average molecular weight and molecular weight distribution determined by GPC using polystyrene standard.
![]()
Figure 1. Figure showing effect of Al/Zr ratio on activity.
![]()
Figure 2. Figure showing effect of Al/Zr ratio on molecular weight.
![]()
Table 3. Table showing homopolymerization results of propylene at different timesa.
aPolymerization conditions: Solvent = Toluene, total volume 50 ml, Zr = 5 µml, bActivity in kg-polymer/mol Zr.hr, cNumber average molecular weight and molecular weight distribution determined by GPC using polystyrene standard.
![]()
Figure 3. Effect of polymerization temperature at Al/Zr ratio 2000.
![]()
Figure 4. Effect of polymerization time at 10 atm.
Comparing run 13 and 14, the yield increased slightly when the polymerization time was increased from 10 to 20 minutes, the activity reduced since the polymerization time was lengthened and there was a slight increase in the molecular weight. The reason for the observed results could have been due to the fact that the catalyst was active for the first 10 minutes and after that there was very little activity and that was why the yield didn’t increase much nor did the molecular weight. Comparing run 15 and 16, there was an increase in the yield when the polymerization time was increased. Comparing the activities, there was no significant difference in the activities, the molecular weight however increased when the polymerization time was increased from 5 to 10 minutes and this could have been attributed to the increase in chain length as more monomers were added to the growing chain with continuing polymerization. Comparing run 17, 18 and 19, the yield and the activity increased when the polymerization time was increased but at 10 atm pressure increase of polymerization time lowered the molecular weight and this could be due to increased chain transfer reactions occurring with increased rates of activity.
3.4. Effect of Polymerization Pressure
The effect of polymerization pressure was investigated by changing the polymerization pressure at the same polymerization conditions, i.e. same Al/Zr ratio and time. The following runs were compared as they had the same polymerization conditions but varying polymerization pressures, (Run 12 and 18 & run 2 and 19). The polymerization results were heavily dependent on the polymerization pressure, as depicted in Table 4. Comparing run 12 and 18, the activity increased when the pressure was increased from 1 atm to 10 atm and so was the molecular weight. When run 2 and 19 were compared the activity increased when the pressure was increased from 1 atm to 10 atm but there was no significant difference in the molecular weight. A general conclusion we could draw from this results is that an increase in polymerization pressure has an effect of increasing the polymerization activity but not necessarily the molecular weight.
4. Conclusion
Propylene homopolymerization has been studied at different polymerization conditions. The results indicate that the activity of polymerization increases with the Al/Zr mole ratio increase and reaches a maximum value at a particular mole ratio. If the mole ratio is increased beyond this point, the activity usually remains constant, or decreases slightly. It was noted that the activity increased with increase in polymerization time. When the concentration of Al/Zr was increased, the molecular weight increased until a Al/Zr mole ratio of 3000 had been reached. When a higher Al/Zr ratio of 4000 was used, a slight decrease was observed. Consequently, the molecular weight was also dependent on the polymerization time. The molecular weight increased when the time was increased since more monomers were added to the growing chain and this led to an increase in the molecular weight. However at 40˚C, the molecular weight decreased when the time was increased. The molecular weight was dependent on the polymerization temperature and was highest at 0˚C reduced at 25˚C and was
![]()
Table 4. Table showing homopolymerization results of propylene at different pressuresa.
aPolymerization conditions: Solvent = Toluene, total volume 50 ml, Zr = 5 µml, bActivity in kg-polymer/mol Zr.hr, cNumber average molecular weight and molecular weight distribution determined by GPC using polystyrene standard.
lowest at 40˚C. The reason for this could be that as the temperature increases, the chain transfer reactions increase and this has an overall effect of lowering the molecular weight. It was also evident that an increase in polymerization pressure has an effect of increasing the polymerization activity but not necessarily the molecular weight.
Acknowledgements
This work is derived from part of the work I did under the supervision of Prof. Cai Zhengguo, Donghua University, Shanghai, China. The work was supported by National Natural Science Foundation of China (21174026), Program for New Century Excellent Talents in University, the Program for Professor of Special Appointment (Eastern Scholar) at Shanghai Institutions of Higher Learning, “Shu Guang” project supported by Shanghai Municipal Education Commission and Shanghai Education Development Foundation.