1. Introduction
It is well known that the diesel engines are well recognized for their reliability and efficiency which well established position in commercial vehicles and industrial application because of their wide usages in passenger cars and in the transportation field generally. Diesel engineering is becoming a fast growing applied engineering discipline to meet the demands for designing optimum diesel engines in relation to greater efficiency and power, low noise, acceptable emissions, greater maintainability and fuel economy [1] . However, like everything in life, there are some factors unfavorable to diesel engines such as low air utilization due to the need for excess air to ensure smoke free combustion, low power to weight ratio, high noise level, and most important of all, the ignition delay problem, which is the time period between the injection of the fuel and the start of combustion. When this delay becomes long, it will lead to the phenomenon of diesel knock; excess fuel injected into the combustion chamber during the delay period and in the combustion process causes more rapid and greater rises in cylinder pressure. This problem will lead to possible losses in the output power, high noise, rough operation and increase in the fuel consumption. One of the major causes of this kind of problem in diesel engines is low ignition quality fuels used in such engines.
In recent years, the increasing demand for diesel fuels has resulted in use of greater percentages of cracked distillates [2] . The problem with such fuels has resulted in the use of greater percentages of cracked distillates. The problem with such fuels derived from cracked distillates is that they have a relatively low cetane rating (i.e. poor ignition quality), which normally requires higher temperature to ignite than their straight-run counterparts [3] . Such fuels need to be improved to have better ignition properties in order to minimize ignition delay problems, also to avoid difficulties in starting engines in cold weather. One of the most common methods used to improve the ignition quality of such fuels is the diesel additives. A famous type of such additives that has been investigated and found to be the most effective is Di-T-Butyle Peroxide (DTBP) and considered to be an effective cetane number improving agent. Organic peroxides and nitrates were also examined BY Al-Rubaie et al. [3] and found to be effective in reducing ignition delay period. He concluded the primary role of additives was that of heat generation through rapid, exothermic, oxidative degradation following injection to the cylinder. They play a major role in the formulation of diesel fuels, and provide a rapid and easy means of improving the fuel’s performance and controlling its quality during production and distribution. The importance of the additives became more over recent years, due to the great concern over the quality of automotive fuels, including governments, public, engine manufactures, and the petroleum industry, because the quality doesn’t only effect the performance of an engine, but also the hazards to health presented by atmospheric pollution from the combustion products of such fuels. Many studies have been conducted on the effect of ignition delay on the diesel engine performance [4] - [11] . They all contend that optimum performance of the diesel engine with respect to power, fuel consumption, noise, and exhaust emissions can only be achieved with good ignition quality fuels. This study investigates the effects of fuel cetane number, initial pressure and temperature and engine speed on the ignition delay in diesel engines.
2. Theory
2.1. Principles of Operations and Performance of Diesel Engines
In the diesel engines, the processes of ignition and combustion start when air is drawn into the cylinder on the downward stroke, during the next stroke, the air charge compressed to a final pressure (= 35 − 50) bar with a final temperature of about 900 - 1000 K. Then fuel is injected by means of a pressure jet atomizer in the form of a fine spray shortly before the end of the compression stroke. After the elapse of the ignition delay, ignition occurs and combustion results at about the compression stroke. At this point pressure may exceed 70 bar and temperature may reach 2800 K. Energy release continues as work is done during the downward expansion stroke. The pressure-crank angle diagram (Figure 1), the compression and combustion process can be divided into three broad stages, to analyze what is actually happening. When the injector starts to inject fuel into the combustion chamber there will be some time elapse before the fuel droplets reach the temperature of ignition. This is represented by the distance, when this takes place, most of the fuel injected during the first stage ignites spontaneously, causing an abrupt pressure rise. The rest of the fuel injected during stage 3 is burnt as soon as it enters the combustion chamber. During the first stage, the fuel is sprayed into the hot air in the cylinder, the fuel droplets are heated up and then vaporized, mixing will take place and hence the mixture will be at this point ignitable, and ready to burn after the ignition lag has elapsed. In the second stage, the fuel injected and prepared for combustion in the first stage now begins to burn and thus causing a very rapid pressure rise, resulting from the sudden burning of the prepared fuel accumulated during the delay period. This is known as knock in diesel engines. In the third stage the burning of the prepared first stage mixture is completed and the burning of the fuel injected in the second and third stages occurs. During this stage the conditions are controlled by the mixing of the rest of the fuel injected with air. From the above, the combustion process can be seen as two portions, physical and chemical portions. During the physical portion of the above processes, fuel injection, fuel jet disintegration, air penetration by liquid fuel, fuel evaporation and mixing of the evaporated fuel with air take place, where in the chemical portion, pre-ignition reactions will take place, which are responsible for generating the required pre-flame oxidation of the hydrocarbons (the liquid fuel) to release energy.
2.2. Parameters that Effect on the Ignition Delay (ID)
The ignition delay period is universally defined as that time interval extending from the start of injection to the onset combustion. This ignition delay will cause an increase in temperature inside combustion chamber of diesel engines before
combustion commences and consequently, will cause pressure to increase, which will lead to undesirable autoigniton. This will result in knock phenomenon which is a very high speed pressure waves (shock waves) that may cause a failure of piston walls and piston rings. When fuel first injected it start to atomize, then evaporates, these process govern the physical delay. After that fuel then mixes with the hot air in the cylinder where chemical reaction commences relatively slowly, which governs the chemical delay in the ignition process. The reaction then rapidly accelerates until “ignition” occurs. An important fact that must be considered in analyzing that ignition delay is the start of injection and the combustion in the cylinder. The start of injection is usually taken as the time when the injector needle lifts off its seat, which is normally determined by a needle-lift indicator. On the other hand, the combustion process is rather more complicated as it is an unsteady three-dimensional process and depends on other parameters such as the fuel, combustion chamber, fuel-injection system, and the operating conditions of a particular diesel engine, such as, late injection timing and low engine speed (rpm) which may also cause ignition delay.
The injection parameters include injection timing, injection pressure, and injection quantity. However, when injection starts early in the engine cycle, it will cause the delay period to be longer because initially pressure and temperature are low and longer time will be required for the pressure and temperature to reach the desired level for ignition. However, if the injection starts late (closer to the TDC), pressure and temperature are initially slightly higher and decrease due to the piston motion. Injection pressure will influence the velocity, drop size and the rate of injection, the effect will depend on the injector nozzle type and the geometry. However, experiments by [8] have shown that none of these factors has a significant effects on the delay, increasing injection pressure at normal operating conditions, will produce only modest decrease in the delay period. The amount of fuel injected have no significant effect on the ignition delay at normal operating conditions, however under engine starting condition, the delay increases with the increase of injection quantity. This is due to the lower temperature associated with increased evaporation for more amount of fuel injected.
However at the starting conditions (speed of engine, compression temperature are low) the effect becomes more important [1] , due to the higher rates of evaporation and mixing associated with swirl. On other hand, the chemical characteristics of the diesel fuel play an important role and hence a strong impact on the ignition delays. The most important factor is the cetane number, as this indicates how readily the fuel self-ignition. Fuels with high cetane number will reduce the ignition delay compared to fuels with low cetane number. A good research has been made [7] , which studies the ignition and combustion characteristics of the principle hydrocarbons found in diesel fuels, and made a better understanding of the relationships between fuel composition and its combustion behavior under divers conditions of utilization. Many investigators have interpreted the starting points of combustion [1] [2] [3] [4] [5] . However, most of them have considered combustion to occur at the point of measurable pressure rise owing to energy release [3] . Others have adapted alternative ways including the start of rapid temperature rise, the point of detectable light emission, and the point of measurable free radical concentration. An important factor that had to be considered in processing the collected file data, is to be aware of the actual starting point of injection. This value is estimated by tracing the injection. More informative details about ignition delay periods in diesel engines can be found in [12] .
3. Mathematical Modeling for Ignition Delay
3.1. Variables and Assumptions
In the present research, theoretical approach is used via a program written in MATLAB [13] , to compute the ignition delay in (ms) for a diesel engine at different operation conditions, by taking different pressures, temperatures, with different compression ratios (rc1:16, rc2:18, rc3:20), different fuel types (CAN = 40, CNB = 50) with different engine speeds such as [1000, 1500, 2100, 2800, 4500, 5500] (rpm). There are some assumptions that have been made as the injection timing taken at top dead center (TDC) and 0.12 m stroke length. The ignition delay in crank angle
will be calculated 300 times at different operation conditions as mentioned previously. First, the mean piston speed
will be calculated 6 times depend on engine speeds [1000, 1500, 2100, 2800, 4500 and 5500]. Then, the activation energy
will be calculated 3 times with each compression ratio (rc1:16, rc2:18, rc3:20) ; the inlet temperature at (TDC) will be calculated 6 times at rc1:16, Also will be calculated 6 times at rc2:18, also will be calculated at rc3:20. and the inlet pressure at (TDC) will be calculated 6 times at rc1:16, Also will be calculated 6 times at rc2:18 and will be calculated at rc3:20, the ignition delay in millisecond
could be calculated.
3.2. Correlation of Ignition Delay in Engines
At the present time, there is no simple complete model of ignition delay. However, an empirical formula, developed by [5] , including assumptions for all equations, to estimate the period of ignition delay in diesel engine has shown to give good agreement for different engines.
(1)
where,
is the ignition delay in crank angle degrees, P is the pressure in bars, and Sp is the mean piston speed m/s,
is the mean piston speed (m/s), R = Universal gas constant (KJ/kmol K), EA is activation energy, where,
is the ignition delay in crank angle degrees, P is the pressure in bars, and Sp is the mean piston speed m/s,
(2)
TTDC = Temperature in K, 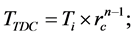
PTDC = Pressure in bar, 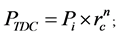
Ignition delay in millisecond, and 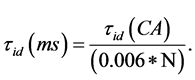
With the same values mentioned previously, the program will take it as input values as: Stroke length (L) = 0.12 m, polytrophic index (n) =1.4.
Temperatures (T) = [T1 = 15, T2 = 20, T3 = 25, T4 = 30, T5 = 35, T6 = 40];
Pressures (P) = [P1 = 1, P2 = 1.3, P3 =1.5, P4 = 1.7, P5 = 2.1, P6 = 2.5];
Engine speeds (N) = [N1 = 1000, N2 = 1500, N3 = 2100, N4 = 2800, N5 = 4500, N6 = 5500];
Compression Ratios (rc) = [rc1 = 16 rc2 = 18 rc3 = 20];
Cetane number (CN) = [CAN = 40, CNB = 50].
4. Results and Discussion
The results were taken by using MATLAB to clarification the influence of operating condition on ID, the results shown (Figures 2-7) are for fuel CN-40
![]()
Figure 2. ID vs. speed for CN-40 at 1 bar & 15 C˚.
![]()
Figure 3. ID vs. speed for CN-40 at 1.3 bar & 20 C˚.
![]()
Figure 4. ID vs. speed for CN-40 at 1.5 bar & 25 C˚.
![]()
Figure 5. ID vs. speed for CN-40 at 1.7 bar & 30 C˚.
![]()
Figure 6. ID vs. speed for CN-40 at 2.1 bar & 35 C˚.
at different intake pressure and temperature (Pi & Ti) for three values of compression ratio (Cr) at different engine speeds. Figures 8-13 show the results for fuel CN-50 at different intake pressure and temperature (Pi & Ti) for three values of compression ratio (Cr) at different engine speed.
Figure 14 shows the effect of cetane number on ID. It is clear from this figure that the ignition delay decreases as the cetane number increases. Figure 15 and Figure 16 show the effect of pressure and temperature on ID at different cetane numbers in 3-D surfaces. The figure clearly shows that ID decreases as the pressure and temperature are increasing, due acetate the chemical and physical factors. Figure 17 shows ID against the engine speed. The figure shows that after the engine speed 7500 RPM, the effect on ignition delay diminished. Figure 18 shows ID against compression ratio for CN 40 & CN 50 at 1 bar & 15˚C. It is so clear
![]()
Figure 7. ID vs. speed for CN-40 at 2.5 bar & 40 C˚.
![]()
Figure 8. ID vs. speed for CN-50 at 1 bar & 15 C˚.
![]()
Figure 9. ID vs. speed for CN-50 at 1.3 bar & 20 C˚.
![]()
Figure 10. ID vs. speed for CN-50 at 1.5 bar & 25 C˚.
![]()
Figure 11. ID vs. speed for CN-50 at 1.7 bar & 30 C˚.
![]()
Figure 12. ID vs. speed for CN-50 at 2.1 bar & 35 C˚.
![]()
Figure 13. ID vs. speed for CN-50 at 2.5 bar & 40 C˚.
![]()
Figure 14. ID vs. speed for CN-40 and CN-50 at 1 bar & 15 C˚.
![]()
Figure 15. ID vs. intake pressure & temperature for CN-40 at 1000 RPM & Cr-16.
![]()
Figure 16. ID vs. intake pressure & temperature for CN-50 at 1000 RPM & Cr-16.
from the previous graphs, at all operating conditions, that ignition delay decreases as the cetane number, compression ratio pressures, temperatures and engine speeds are increased. Moreover, the reduction in ignition delay was more remarkable at lower engine speeds and lower compression ratio.
5. Conclusion
Influence of ignition delay on the diesel engine performance has been investi-
![]()
Figure 17. ID vs. engine speed for CN-40 at 1 bar & 15 C˚.
![]()
Figure 18. ID vs. compression ratio for CN-40 & CN-50 at 1 bar & 15 C˚.
gated using a theoretical model via a program written by MATLAB. An assumption has been made, which states that injection timing taken to be at top dead center and the stroke length of engine to be 0.12 m. The ignition delay in the diesel engines using different reference diesel fuels with different cetane numbers of 40 and 50 was investigated. Effect of the operating conditions such as the engine compression ratios, intake pressures and temperatures on the ignition delay was investigated. Influences of engine speed changes on ignition delay at low, moderate and high conditions were represented. The results concluded that the ignition delay decreases as the engine speed is increased, increasing the fuel cetane number, decreasing the engine ignition delay. Also, the ignition delay de- creases as intake pressure and temperature increase. The compression ratio causes remarkable reduction in ignition delay. It found also that, after the engine speed 7500 RPM, there is no more effect on ignition delay.