Reaction Kinetics Study of Catalytical Hydrogenation of Furfural in Liquid Phase ()

1. Introduction
The liquid phase hydrogenation of furfural is commonly used to produce furfuryl alcohol, tetrahydrofurfuryl alcohol and 2-methylfuran [1] [2] [3]. Furfuryl alcohol is widely used in producing various synthetic fibers, rubbers, resins, and farm chemicals. It can also be used as a good solvent for furan resin, pigment and varnish and as rocket fuel [4]. In the case of hydrogenation of furfural to tetrahydrofurfuryl alcohol in the absence of solvent or in an aqueous solution highly active are the supported nickel catalysts. The hydrogenation of furfural has been carried out in either liquid or vapor phase. Most companies adopt gas phase hydrogenation. However, in some countries, e.g. in China, liquid phase hydrogenation is frequently employed [5]. The catalyst mainly used for furfural hydrogenation in the industry is a Cu-Co catalyst modified with various promoters [6]. As Cu-Co catalysts have high toxicity and thus cause severe environmental pollution, many attempts have been made to develop new catalysts that are environmentally friendly. Applications of PtCu [7], Ru [8], Ni2P [9] have been reported.
This paper describes a study on the catalytic hydrogenation of furfural using Raney Ni, besides an investigation of the effect of reaction time, reaction temperature on the yield of tetrahydrofurfuryl alcohol and the kinetics of this reaction. Provide reference for the industrial application of liquid phase hydrogenation of furfural.
2. Experimental Section
2.1. Experimental Reagents
Furfural (supplied by Shanghai Jinshan Tingxin Chemical Reagent Factory) of purity 99% was used for the preparation of furfuryl alcohol. Hydrogen (supplied by Hangzhou today’s industrial goods and Materials Co., Ltd.) of purity 99% was used for furfural hydrogenation. Raney nickel catalyst (supplied by Shanghai Sun Chemical Technology Co., Ltd.) of an average pore size 3 μm, and surface area 1000 m2/g was used for the hydrogenation of furfural.
2.2. Experimental Apparatus
A schematic diagram of laboratory experimental unit used for the hydrogenation of furfural is shown in Figure 1. This unit consists of a 100 ml stainless steel autoclave equipped with a mechanical stirrer and an electric heating system.
The composition of product is measured by an automatic on-line valve and analyzed with a gas chromatograph (GC) and PEG-30m column and FIT detector. Furfural, furfuryl alcohol and tetrahydrofurfuryl alcohol are identified and quantified with the response factor method using model compounds.
2.3. Experimental Procedure
Catalytic hydrogenation of furfural was performed in a 100 ml stainless steel autoclave equipped with a mechanical stirrer and an electric heating system. 70 ml of ethanol, which were first transferred into the autoclave, were used as the solvent. Then 5 ml of furfural and a mount of Raney nickel catalyst were added to the autoclave. After the necessary connection between the autoclave and hydrogen gas cylinder was duly made, H2 gas passed into the autoclave until H2 pressure reached 1.0 MPa. Then pressurization and successive depressurization were repeated 5 times so as to completely replace the air in the autoclave. Then the reactor was filled with H2 up to the prescribed pressure, followed by heating slowly until the prescribed temperature. The first product sample for analysis was taken after 10 min of reaction (period needed to reach reaction steady-state). After reaction for 3 h, the reaction products were analyzed to determine the conversion of furfural and the selectivity to furfuryl alcohol. The identification
![]()
Figure 1. Schematic diagram of furfural hydrogenation unit. 1: Hydrogen cylinder; 2: Controller; 3: Pulsator; 4: Exhaust head; 5: Pressure gauge; 6: Reactor; 7: Bleeder valve; 8: Needle valve.
and analysis of the reaction product mixtures were performed by means of GC. Conversion of furfural was measured directly by the comparison of its concentration in the inlet stream with the outlet stream. Selectivity was calculated as the ratio of the number of moles of tetrahydrofurfuryl alcohol to number of moles of all products formed in the reaction.
3. Results and Discussion
3.1. Reaction Pathways of Furfural Hydrogenation in Liquid Phase
As shown in Scheme 1, the formation of furfuryl alcohol and tetrahydrofurfural are parallel reactions, which are competitive, while tetrahydrofurfuryl alcohol is the final product of further hydrogenation of both furfuryl alcohol and tetrahydrofurfural.
In the process of catalytic hydrogenation of furfural to tetrahydrofurfuryl alcohol, the sample was taken out and analysis by GC-MS, Figure 2 shows that products of sample comprise furfural, furfuryl alcohol and tetrahydrofurfuryl alcohol. It has been claimed that reaction pathway for furfural catalytic hydrogenation was form furfuryl alcohol first then to tetrahydrofurfuryl alcohol.
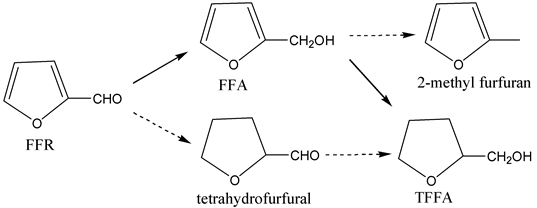
Scheme 1. Reaction pathway for furfural catalytic hydrogenation, (...) possible pathway; (-) actual reaction pathway.
![]()
Figure 2. GC-MS analysis of the products.
3.2. Effect of Stirring Rate
Figure 3 shows that the effect of stirring rate on furfural hydrogenation reaction under the reaction conditons. It shows that the yield of tetrahydrofurfuryl alcohol increases with increasing stirring rate. However, the influence of stirring rate becomes weak when the stirring rate reaches 450 r・min−1.
![]()
Figure 3. Effect of stirring rate on furfural hydrogenation reaction. Reaction conditions: T = 383 K; P = 1.5 MPa; t = 180 min; m (cat.) = 2.0 g.
3.3. Effect of Reaction Time
Figure 4 shows the effect of reaction time on the conversion of furfural and the selectivity for tetrahydrofurfuryl alcohol. It shows that, within 40 min of reaction time, the conversion increases to 100%, while the selectivity raises slowly. As reaction time is prolonged, the selectivity increases to more than 80% and then falls appreciably. This could be attributed to the fact that some compounds derives from hydrogenation of tetrahydrofurfuryl alcohol.
3.4. Effect of Reaction Temperature
Increase in temperature of a reaction usually causes an increase in reaction rate. From Figure 5, it is seen that as the reaction temperature is increased, the selectivity for tetrahydrofurfuryl alcohol increases obviously at temperature below 403 K. However, the selectivity for tetrahydrofurfuryl alcohol falls when the reaction temperature rises to 418 K. This could be attributed to the fact that many other compounds derived from secondary reactions, such as hydrogenolysis of the C-O bond, decarbonylation, hydrogenation and furan ring opening, may appear.
3.5. Hydrogenation Kinetics
Determination of reaction order
For the determination of the order of reaction, equations of zero-, first- and second-order reactions was used. These equations can be written as follows:
Zero-order reaction equation:
(1)
![]()
Figure 4. Conversion of furfural and selectivity for tetrahydrofurfuryl alcohol as a function of reaction time. Reaction conditions: T = 433 K; P = 1.5 MPa; m (cat.) = 2.0 g.
![]()
Figure 5. Influence of reaction temperature on selectivity for tetrahydrofurfuryl alcohol. Reaction conditions: P = 1.5 MPa; t = 180 min; m (cat) = 2.0 g.
First-order reaction equation:
(2)
Second-order reaction equation:
(3)
Table 1 shows time against furfural concentration data using 2.0 g catalyst at a temperatures of 373, 378, 383, 388 and 393 K.
Plot of (FFA) and [1/(FFA)] vs. time for Equations (1) and (3), respectively are nonlinear as shown in Figure 6 and Figure 7, while plot of Ln((FFA)0/(FFA)) vs. time for Equation (2) is linear as shown in Figure 8. This proves that the furfural hydrogenation follows the first-order nature.
Table 2 shows time against tetrahydrofurfuryl alcohol concentration data using 2.0 g catalyst at a temperatures of 373, 378, 383, 388 and 393 K.
Plot of (TFFA) vs. time for Equation (1) respectively is linear as shown in Figure 9. This proves that the furfuryl alcohol hydrogenation follows the zero-order nature.
![]()
Table 1. Time vs. furfural concentration data.
![]()
Figure 7. Test for second-order reaction.
![]()
Table 2. Time vs. tetrahydrofurfuryl alcohol percentage concentrations.
![]()
Figure 8. Test for first-order reaction.
3.6. Determination of Activation Energy
The activation energy is calculated by the use of Arrhenius equation which can be written as follows:
(4)
The first-order reaction rate constant calculated from Equation (2) and Figure 8 at different temperatures is shown in Table 3. Figure 10 shows a plot of Lnk1 vs. [1/Temp.](1/K). Linear equation is obtained with slope of (E/R), and activation energy is calculated as 24.7 kJ/mol.
The zero-order reaction rate constant calculated from Equation (1) and Figure 9 at different temperatures is shown in Table 4. Figure 11 shows a plot of Lnk2 vs. [1/Temp.](1/K). Linear equation is obtained with slope of (E/R), and activation energy is calculated as 27.7 kJ/mole.
![]()
Table 3. Effect of temperature on furfural hydrogenation.
![]()
Figure 10. Effect of temperature on reaction rate.
![]()
Table 4. Effect of temperature on furfuryl alcohol hydrogenation.
![]()
Figure 11. Effect of temperature on reaction rate.
4. Conclusions
1) Below the stirring speed of 450 r・min−1, the yield of tetrahydrofurfuryl alcohol increases with increasing stirring rate.
2) A maximum tetrahydrofurfuryl alcohol yield of 96% is obtained at a 180 min reaction time, 383 K reaction temperature, 1.5 MPa H2 and 2.0 g catalyst.
3) The corresponding order is first-order with respect to furfural concentration and zero-order with respect to tetrahydrofurfuryl alcohol concentration for the hydrogenation of furfural and the hydrogeoxygenation of furfuryl alcohol, respectively.
4) The corresponding values are 24.7 kJ/mole and 27.7 kJ/mole for the hydrogenation of furfural (E1) and the hydrogeoxygenation of furfuryl alcohol (E2), respectively.
Acknowledgements
The authors greatly thank the financial support from the Science and Technology Department of Zhejiang Province of the People’s Republic of China (No.2005C12023; No. 2011R09028-10; 2009R50028).
Notation
E: activation energy (kJ/mol)
k: reaction rate constant
k1: first-order reaction rate constant (min−1)
k2: zero-order reaction rate constant (gmole/liter/min)
T: temperature (K)
t: time (min)
R: gas constant (8.314 J/gmole/K)
FFR: furfural
FFA: furfuryl alcohol
TFFA: tetrahydrofurfuryl alcohol
CA,0: initial concentration of component A in reaction solution (mol/mL)
CA: final concentration of component A in reaction solution (mol/mL)